サイト内の現在位置
イノベータ’s VOICE
「チョコ停」が減らないのは、手書きが原因だった?
改善活動で成果を出す簡単な方法とは
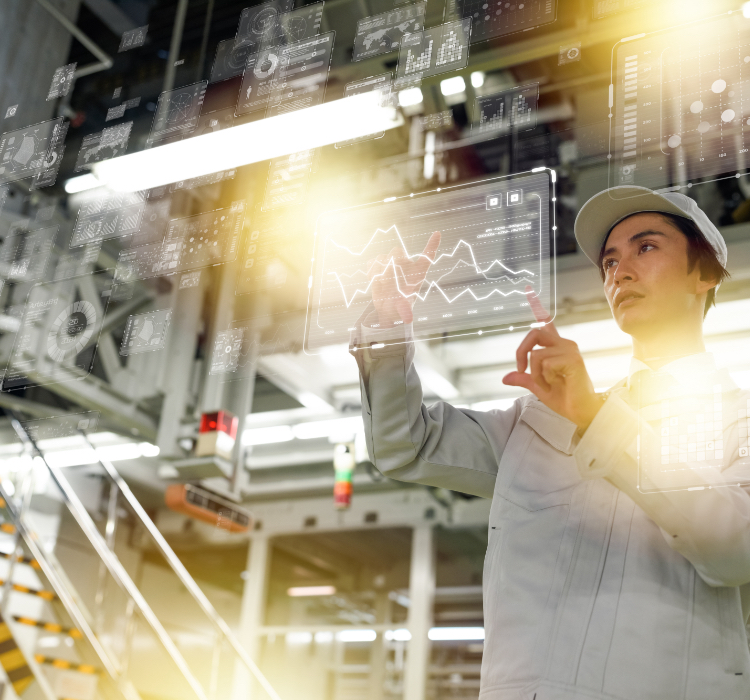
UPDATE : 2021.09.03
製造業の工場など、多くの製造現場を悩ませている「チョコ停」。文字通りすぐに復旧可能な製造設備の停止を意味するのですが、リカバリーが容易であることが問題解決を先送りにし、結果として多くのロスを招いているという現状があります。ここでは、そんなチョコ停が起きる原因から、最新のIoT技術を駆使したチョコ停対策までを解説します。
INDEX
- 製造ラインの生産性向上をはばむ「チョコ停」とは
- チョコ停はなぜ起きる?なぜ見逃される?
- 清掃や定期メンテナンスの不足
- ラインバランスが不適切
- 前工程の作業品質がまちまち
- センサー類の読み取りエラー
- チョコ停回避の第一歩は正確なデータの収集
- IoTを活用し、簡単・正確に情報収集
改善効果でチョコ停時間を2割削減 - 常時監視でトラブルを即通知するので早期解決が可能
- まとめ
製造ラインの生産性向上をはばむ「チョコ停」とは
製造業の工場などの現場で耳にすることの多い「チョコ停(ちょこてい)」という言葉。これは「チョコっと停止」を縮めた言い回しで、文字通りラインなどの製造設備がわずかな時間だけ停止してしまうトラブルを表します。これに対して、大規模な設備停止は「ドカっと停止」から「ドカ停」と呼ばれます。
実はこの言葉、可愛らしく聞こえるのですが、JIS(日本産業規格)にもその名前が登場するれっきとした生産管理用語。あくまで「小故障」の通称という扱いではありますが、公的に使われることも多い、一般的な表現です。
- 設備が生産ラインなどの大規模なシステムの一部となっていて、システム全体を停止に至らしめるような重大又は決定的な故障を大故障(通称としてドカ停)、逆に設備の部分的な停止又は設備の作用対象の不具合による停止で、短時間に回復できる故障を小故障(通称としてチョコ停)という
- 出典:JISZ8141:2001 生産管理用語 | 日本産業規格の簡易閲覧
多くの製造現場にとってチョコ停は日常茶飯事。実際に製造現場で働いたことのある人なら、こうした短時間の設備停止が毎日何度も起きていることを熟知しているはずです。その原因はラインの詰まりや引っかかり、想定外の異物混入など、軽微なものがほとんどで、現場の作業員が原因を取り除き次第、すぐに(数十秒~数分程度で)正常な状態に復帰することができます。
しかし、この数分程度のロスも積もり積もれば大きなロスになります。また、チョコ停が発生したことを監視する仕組み作りや、そのための人員確保なども大きなコスト負担に。何より、チョコ停が頻繁に発生する製造現場にはドカ停に繫がる潜在リスクがあると言えるため、見過ごすわけにはいきません。
チョコ停はなぜ起きる?なぜ見逃される?
では、チョコ停はどうして起こるのでしょうか? 代表的な原因として、次のようなことが挙げられます。
清掃や定期メンテナンスの不足
金属や木材の加工時に発生する削りくずをそのままにしておくなど、設備の清掃を怠ると、それによって工作機械が正常に動作しなくなりチョコ停を引き起こすことがあります。また、定期的なメンテナンスの不足により引き起こされる設備停止のうち、修理を伴わずに復旧できるものもチョコ停とされます。
ラインバランスが不適切
製品や部品、材料が流れる製造ラインのバランスが取れていないこともチョコ停を引き起こす原因となります。何を、どのくらいの数、どのくらいの速度でラインに流すかなど、適切な設計ができていないラインは行程上で詰まりや引っかかりなどを起こしがちです。
前工程の作業品質がまちまち
加工品の製造工程では、前工程で加工された材料の品質が低かったり不揃いだったりすると、それを受けて作業する次工程でのチョコ停リスクが大幅に高まります。不良品をあらかじめ選別し、ラインに流れないようにするなどといった対策が必要です。
センサー類の読み取りエラー
ライン上を流れる製品や部品、材料をチェックするセンサー類は、環境や経年劣化などの要因で認識精度が低下することがあります。こうしたセンサー類の読み取りエラーもチョコ停の原因の1つです。
これらのチョコ停は、現場の作業員によって即再開できてしまうため、どうしても原因の究明は後回しになってしまいがちです。また、どういうチョコ停があったのかという記録も、作業員が動き出した製造ラインの監視に戻らなければならないために滞りがち。結果として、だらだらとチョコ停と付き合い続けることになってしまいます。
チョコ停を減らすためには、まず、「いかにチョコ停を顕在化するか」が重要です。
チョコ停回避の第一歩は正確なデータの収集
では、チョコ停を顕在化するには何をすれば良いのでしょうか。まず取りかかるべきは、チョコ停の理由と発生した時刻、再開した時刻を正しく記録することです。しかし、現実問題として多くの現場では、その都度ごとに記録するのは容易ではありません。
また、記録している現場でも、チョコ停を台帳やホワイトボードなどに手書きで記録していることが多く、ミスや誤記の温床になっています。特に繁忙期などはライン稼働率を高めることに意識が行ってしまい、正確な記録を残すことが後回しに。そして、そのまま失念されてしまうことも多いでしょう。そうした手書きの情報を集計する手間も無視できません。
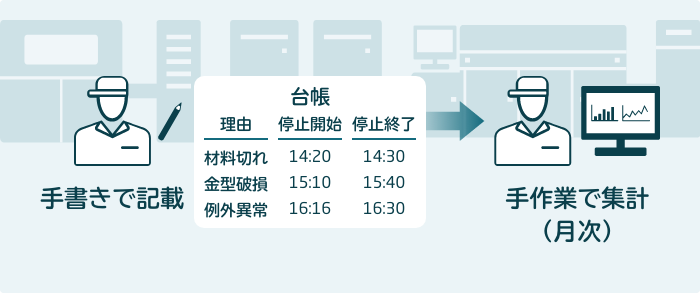
逆に言えば、チョコ停改善のカギはそこにあるのです。
IoTを活用し、簡単・正確に情報収集
改善効果でチョコ停時間を2割削減
台帳やホワイトボードに手書きでチョコ停の状況を記録していくことがミスや誤記の温床となり、集計効率の面でも問題があることは前段でも説明しました。
では、現場にパソコンやタブレットを設置して、チョコ停が起こる度に入力していく方式にするのはどうでしょうか? これであれば、少なくとも集計の手間は大きく軽減できそうです。しかし、記録の手間はそれほど軽減できないでしょう。作業員のITリテラシーが高くない場合、手書きよりも誤記のリスクが高まり、入力に要する時間も長くなってしまうかもしれません。
そんな中、注目を集めているのがIoT(Internet of Things)を活用した取り組みです。NECソリューションイノベータでは、これまでの方式に近い、ホワイトボードとマグネットを使ったソリューションを提供しています。「材料切れ」などの停止理由が記載された複数のマグネットセンサーがホワイトボードに並べられており、作業員はチョコ停が起こる度に、該当するマグネットセンサーに小さなマグネットを貼り付け、その後ラインが復旧したらマグネットを取り外します。
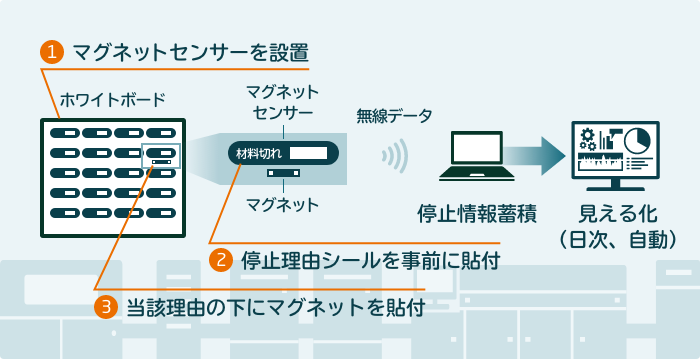
それぞれのマグネットセンサーにはIoTの機能が組み込まれていて、どのマグネットセンサーにマグネットが貼られたか(=停止理由)、マグネットを貼り付けられた時刻、取り外された時刻(=停止期間)がサーバーに送信されます。
このソリューションの優れた点は、作業員に特殊な技能が求められないこと。また、製造ラインの状況が担当作業員以外にも一目で分かり、データ化が正しく、手間なく行えます。これによって作業員は本来やるべき作業に集中できます。
その結果、このソリューションを導入したある企業では、データ収集と集計作業の工数が6分の1にまで削減。その後、データ分析を元にした改善によって停止時間を約2割も削減することができたと言います。
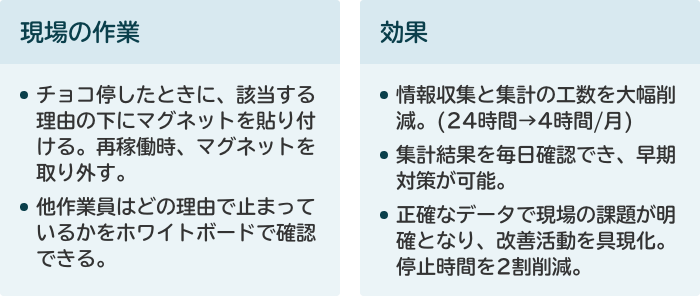
常時監視でトラブルを即通知するので早期解決が可能
前段で紹介したソリューションでは、IoTをデータの収集部分に活用することで大きな成果を上げていましたが、チョコ停の監視そのものは人が目視で行っています。そのため、大規模な製造設備では、トラブルの発生を認識するまでに時間がかかってしまうという問題がありました。
そこで、こうしたトラブルの発生までを各種センサーを駆使して常時監視しようという取り組みも始まっています。NECソリューションイノベータの製造現場通知ソリューションでは、トラブルの発生をセンサーが感知すると、即座に担当者に通知されます。また、そこでどのような対処を行ったかも記録されるため、後日、一連の動きをふり返ることも可能です。
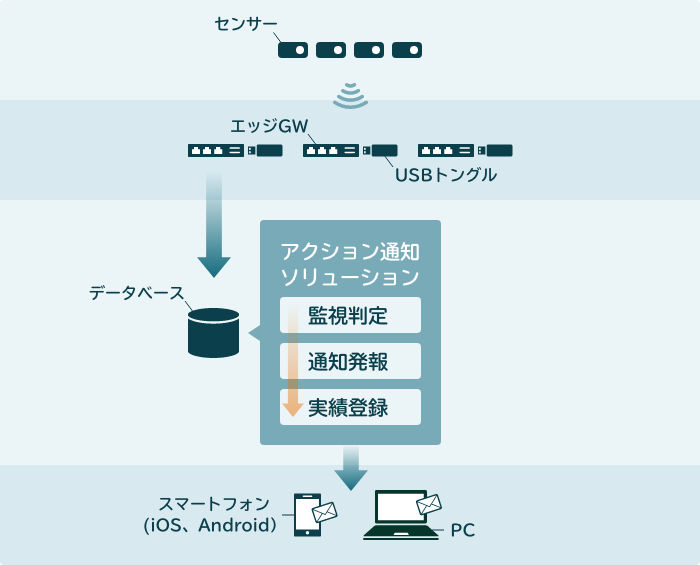
まとめ
多くの製造現場を悩ませているチョコ停。その解決には多くの手間がかかると思われていましたが、昨今ではIoTなどの先端IT技術を駆使することで、原因究明や問題解決がしやすくなっています。こうした仕組みを導入する費用もどんどん下がっており、また、蓄積したデータを可視化するサービスも月額数万程度から利用可能です。
こうした時代にいつまでも人間の目と手で設備稼働率を維持しようするのはナンセンス。ITを利活用して高効率な設備稼働とコストの低減を目指しましょう。
関連ソリューション・サービス