サイト内の現在位置
コラム
4Mとは?変更管理と分析方法の基本を解説
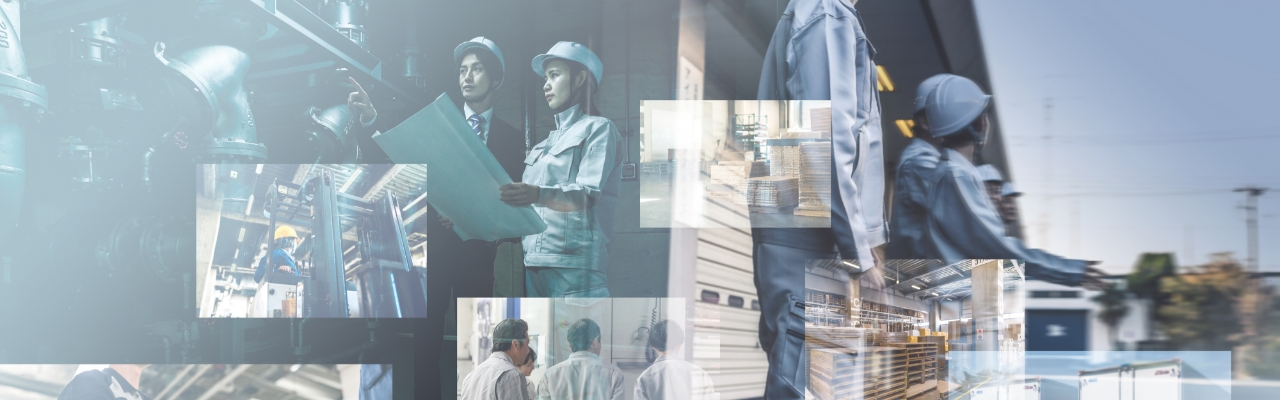
UPDATE : 2022.05.20
4M(よんえむ)とは、Man(人)、Machine(機械)、Material(材料)、Method(方法)の4つの要素を分析・改善していくことで、課題発見や問題解決を図る手法です。製造現場をはじめ、さまざまな場面で活用されています。本記事では4Mの基本と、4Mを適切に活用していくためのポイントをわかりやすく解説します。
INDEX
- 4Mとは
- Man(人)
- Machine(機械)
- Material(材料)
- Method(方法)
- 製造業の業務改善を支えるフレームワーク
- 4Mに要素を追加した「5M+1E」と「6M」
- 製造業の重要キーワード「QCD」
- 安全工学における「4M」
- 4Mを用いた変更管理
- 具体的な変更管理の流れ
- 製造工程を整理する「QC工程表」とは
- 課題を可視化する「QC7つ道具」と「新QC7つ道具」とは
- 4M管理の効果を高めるために
- 4M×3H、4M×5Eで管理する
- AIやIoTなど最新技術の導入
- まとめ
4Mとは
4Mとは、Man(人)・Machine(機械)・Material(材料)・Method(方法)の4要素の頭文字を取って名付けられたフレームワークです。4Mを用いることで、よりMECEに状況を分析できるため、品質管理および製造オペレーションの改善や生産ロス対策の立案に重宝されています。製造業では欠かせないフレームワークであるほか、物流業などの他業種における応用も進んでいます。
昨今では、消費者ニーズが細分化され多岐にわたり、OEMを駆使して多くのプレーヤーが市場参入しています。消費者ニーズに応えるべく多品種少量生産を実施する工場では、4Mが目まぐるしく変化するため、徹底した管理が不可欠です。また、OEMやファブレス生産などの製造委託先の見極めにおいて、4Mの管理状況が重大な選定要因になります。日本の製造業を支えてきたフレームワークである4Mは、昨今の状況下でも変わらず重要で、品質管理の軸として機能しているのです。
ここでは、製造現場における4Mについて、それぞれの要素を解説します。
Man(人)
Manとは、製造現場における“人(作業者)”に関わる要素です。残りのM(Machine・Material・Method)も作業者の影響を大きく受けるため、4Mの中でも特に重要な要素と言えるでしょう。Manに関わる領域で品質に影響するものには、業務の習熟度や勤務状況があります。また、作業に対する人員の過不足や作業品質を維持する教育システム、ヒューマンエラーに大きく影響するモラルやモチベーションなども管理すべきポイントです。
Machine(機械)
Machineとは、製造現場における機械工具や設備機器などの“機械”に関わる要素です。製造現場において生産性と作業品質、製造品質を担保するためには、適切な機械の導入が欠かせません。そのため「最適な機械が導入されているか、正常に機能しているか、老朽化や劣化していないか、不足していないか」などの観点が品質管理に求められます。また効果的に各機械を活用するための設備レイアウトも、重大なMachineの要素です。
Material(材料)
Materialとは、製造現場における“材料”に関わる要素です。製造現場では、製造工程で扱う多種多様な原材料や加工品を正しく管理することが必要です。また、原材料由来の問題が発生した時のために、トレーサビリティを確保することもポイント。「どの業者から仕入れ、どのような製造工程を経て、どのように管理され、どのロットに使用されているか」を明確にすることで、リスク管理を強化できます。そのためMaterialには、材料不足や余剰在庫を発生させないための適正な在庫管理のほか、仕入れ先や調達・受入れ手段の管理なども含まれます。
Method(方法)
Methodとは、製造現場における“方法”に関わる要素です。具体的には、見込み生産や受注生産などの生産形態、ライン生産やセル生産、ジョブショップ生産などの生産方式、作業手順やルール、加工条件や検査・測定方法などが該当します。これらのMethodは、人・機械・材料の要件を適切に組み込み全体最適化されていることがポイント。エラー防止や正当性、生産性、安全性、効率性といった観点で標準化し、属人化を防ぐマニュアルに落とし込む必要があります。また、運用を遵守しているか、運用が適切であるかの状況確認も徹底すべきです。Methodを形骸化させないためにも、継続的な見直しやチェックを実施する管理体制の構築が肝要です。
製造業の業務改善を支えるフレームワーク
ここでは、4Mと並んで品質管理で広く用いられているフレームワークについて紹介します。
4Mに要素を追加した「5M+1E」と「6M」
5M+1E とは、4Mに、Measurement(計測)とEnvironment(環境)を加えたフレームワークです。Environmentには温度、湿度、振動、明度、気圧などが該当します。Measurementは、環境も含めた諸条件の測定および検査に関する要素です。計装機器や計測機器の精度、測定方法や条件、測定マニュアルなどを適正化し、環境などの諸要素を定量的に管理します。また、ゲージR&R分析などのMSA(測定システム解析)を活用して、測定自体の正確性をチェックすることも重要です。
6Mとは、5MにManagement(管理)を加えたフレームワークです。多品種少量生産の現場では小ロットの生産が求められ、製造ラインや製造プロセスが複雑化します。そうした状況下では、各製造工程やリソース配分を最適化するために、全体をコントロールする管理能力が要求されます。また中長期的な視野でのマネジメント計画は、OEMなどで製造委託先を評価・選定する際に注視される要件です。Managementは、製造現場はもとより将来的な企業戦略にも大きく影響を与えることを留意しましょう。
製造業の重要キーワード「QCD」
QCDとは、Quality(品質)、Cost(コスト)、Delivery(納期)の3要素を示す言葉で、4Mと並ぶ品質管理の重要キーワードとして知られています。例えば品質を追求しすぎるとコストと納期を圧迫するように、QCDの3要素はそれぞれトレードオフの関係にあります。そのため、いずれかに偏重することなく、適切なバランスで管理することが求められます。製造現場で4Mによる管理を追求していくにあたり、成果指針としてQCDを追求することが効果的です。実際に運用する際には、QCDそれぞれに定量的な目標値を設定し、継続的に管理します。
なおQCDの派生形として、Service(サポート・顧客対応)を追加したQCDSや、Flexibility(柔軟性)を追加したQCDFといったフレームワークもあります。さらに建設業界ではSafety(安全性)を追加したQCDSや、Environment(環境)を加えたQCDSEが活用されています。いずれも業態に合わせ、QCDから発展させて追求すべき指標を定めています。
安全工学における「4M」
工業分野や、医学、社会生活などにおける安全追及やリスクアセスメントを旨とする安全工学において、4M分析と呼ばれる手法があります。安全工学の4M分析では、Man(人的要因)、Machine(設備的要因)、Media(作業的要因)、Management(管理的要因)でリスク要因を分類し分析。製品事故や品質事故、ヒューマンエラーに向けた未然防止・拡大防止・再発防止策の立案につなげます。
下記は、安全工学における分類の具体的な要因例です。
Man(人的要因):
危機感の欠如などの心理的要因、睡眠不足などの生理的要因、職場の人間関係など
Machine(設備的要因):
道具・機械・設備における設計上の欠陥や不良、点検整備不足など
Media(作業的要因):
不適切な作業方法、作業動作の欠陥、作業環境条件の不良など
Management(管理的要因):
組織体制や監督体制・教育体制、健康管理体制、人員配置計画など
4Mを用いた変更管理
4Mを用いた変更管理は、かねてより日本の製造業で品質管理と品質向上のために取り入れられてきました。現在では、国際的な品質マネジメント規格であるISO9001:2015に「変更の管理」という項目が定められており、4Mによる変更管理の国際的な普及が進んでいます。
●具体的な変更管理の流れ
4M変更管理(あるいは4M変化点管理)とは、製造業の各プロセスにおいて、4Mの変更(変化点)を管理することで製品の品質を保つ取り組みのことを言います。下記は具体的な変化点の例です。
Man(人):
作業担当者・検査員の変更、職制の変更、増員や残業、欠勤や事故など
Machine(機械):
機械の変更・故障・異常検知・劣化・修理・交換、停電など
Material(材料):
設計の変更、原材料の変更、仕入れ先の変更、異物の混入や不良など
Method(方法):
製造工程の変更、操作方法の変更、加工条件の変更、保存管理方法の変更など
上記のような変化点を、過去事例や他社事例なども参照して洗い出し、優先順位を付けます。優先順位を決める際は、品質および他プロセスに与える影響度合いや変化点の発生頻度、推定される損失の大きさなどから評価します。変化点は多岐にわたるため、大前提として変化点を多発させない工程に改善していくことも肝要です。変化点を抽出した後は、変化点が影響を与える範囲を明確にし、記録方法を含めた対処方法やルール、変化点の状態を「見える化」するための管理方法を策定します。
4Mの変更管理は、原則として不良製品の発生や流出を防ぐための取り組みですが、突発的に生じる“予測できない”事態は起こり得ます。そのため、異常や潜在的不良(ヒヤリ・ハットなど)が発覚した際の報告ルールや、暫定的な対応方法を定めることが不可欠です。また実際に異常が発生した場合は、原因究明と再発防止策の立案、再度標準化するための作業員への共有・再教育を徹底します。
継続的な改善を意識してSDCA(Standardize:標準化⇒Do:実行⇒Check:検証・評価⇒Action:改善)を回転させていくことが求められます。
●製造工程を整理する「QC工程表」とは
4M変更管理のベースとして機能するのがQC工程表(QC=Quality Control)です。QC工程表とは、1つの製品の全工程(原材料の入荷から製造、出荷までの工程)の流れと、各工程における品質の管理方法や基準値、責任者などの情報を明記した図表です。QC工程表に決まった様式はないものの、下記の項目が必要とされています。
- 工程の流れ(全製造工程および作業名、工程のフローチャート)
- 工程の管理項目(品質に影響する加工・製造の条件、品質の評価につながる特性値)
- 工程の管理方法(機械・設備・材料、管理者の条件、検査・測定方法、記録方法、異常時の対処方法)
“管理項目”の品質に影響する加工・製造条件(管理特性とも言われます)とは、機械の回転数や加熱温度などが該当します。品質の評価につながる特性値(品質特性と言われます)とは、製造工程の結果である製品の形状や寸法、重量などです。これらの数値の基準を適切に設定し、定量的に管理することが、製造品質のばらつきを抑え高い品質を保つための要件です。
4M変更管理において、製造工程を管理するためにQC工程表は作成されます。そのため工程で異常が発生した場合は、QC工程表に基づく作業が行われているかを確認しなければなりません。もし基準を守って工程を進めたにもかかわらずエラーが発生した場合は、QC工程表の項目を見直して工程を改善する必要があるでしょう。
なおQC工程表には製造工程において品質を担保するための要点が明記されているため、各工程の詳細な作業手順を示す作業標準書の基となるほか、ISO9001で求められる品質計画書に相当する資料にもなります。それゆえ取引先に向けた製造体制の説明にも有用です。より効果的に機能させるためにも、JIS規格(JIS Z8206)で定義された工程図記号を用いて「加工」や「数量検査」などの工程フローチャートを制作するべきでしょう。
●課題を可視化する「QC7つ道具」と「新QC7つ道具」とは
「QC7つ道具」と「新QC7つ道具」は、4M変更管理における課題の「見える化」を助ける手段として、製造業で普及しているツールです。
QC7つ道具 | 新QC7つ道具 |
---|---|
グラフ チェックシート パレート図 ヒストグラム 管理図 散布図 特性要因図 層別 |
アローダイアグラム法 マトリックス図法 マトリックスデータ解析法 系統図法 親和図法 連関図法 PDPC法 |
QC7つ道具とは、グラフ、チェックシート、パレート図、ヒストグラム、管理図、散布図、特性要因図、層別のことです。なお、管理図がグラフに内含されているケースや、層別が抜けているケースもあります。製造現場で収集される定量的なデータの整理や分析、事象間の関連性解明に活用されています。
新QC7つ道具とは、アローダイアグラム、マトリックス図法、マトリックスデータ解析法、系統図法、親和図法、連関図法、PDPC法のことです。英訳のNew Quality Control-7 Toolsを略してN7とも言われています。定性的な言語データを分析することで問題解決へつなげる点が、QC7つ道具との違いです。また、言語データを主に取り扱うため、製造業以外のサービス業などでも活用が進んでいます。
ここではQC7つ道具の1つである特性要因図をピックアップして紹介します。
その図形からフィッシュ・ボーン(魚の骨)図とも呼ばれる特性要因図は、視覚的に情報を整理することで課題の原因究明に貢献します。
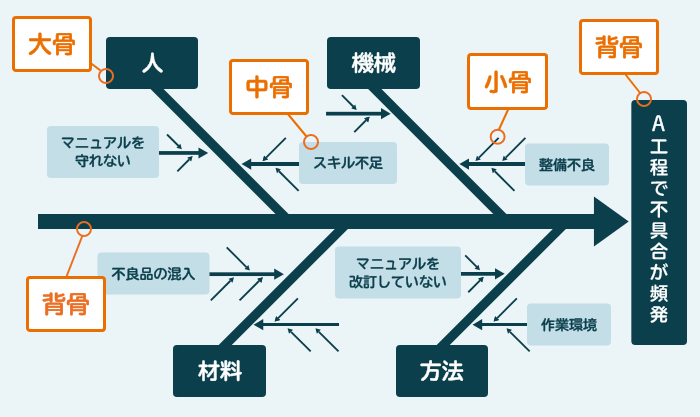
「背骨」に解決すべき課題や特性を置き、その要因となる要素を「大骨」「中骨」「小骨」と掘り下げて考察していきます。特性要因図に4Mの観点を取り入れMECEに課題を分析することで、工程の問題点を視覚的かつ段階的に把握でき、状況の「見える化」促進に有効です。また、要点が明確な図解であるため、社員間での問題意識の共有と標準化にも寄与します。
4M管理の効果を高めるために
4M管理は、新たな着眼点の取り込みや最新技術の活用によって、今日も進化を続けています。ここでは4M管理をより効果的に機能させるための取り組みを紹介します。
4M×3H、4M×5Eで管理する
3Hとは、ヒューマンエラーが起こりやすい状況(変化点)である「初めて、変更、久しぶり」の3つのHを表す標語です。3Hを4Mに組み合わせることで、“重点的に注意すべきタイミング”という軸を品質管理にもたらします。例えばManの場合は「初めて=新入社員、変更=配置転換・人事異動、久しぶり=現場復帰」などが該当し、未然防止に有用な変化点の抽出を助けます。
5Eとは、教育(Education)、技術(Engineering)、強化・徹底(Enforcement)、模範・事例(Example)、環境(Environment)を示します。発生した問題や課題への対策を講じる際に5Eを用いることで、有効な視点を獲得できます。未然防止には3Hを、対策立案には5Eを活用することで、4Mの分析深度を増すことができるでしょう。
AIやIoTなど最新技術の導入
4Mを効率的・効果的に管理するため、IoTを始めとしたデジタル技術の活用が普及しています。例えばIoTのセンシング技術により、人や機械の稼働状況を正確に把握することで、リアルタイムに4M変化点を管理できます。そのほかAIも製造工場での活用が進んでいる技術の1つです。AIを活用して動画や静止画像を識別し、製造ラインでの不良品検出に活かす技術が実現しています。またIoTセンサーで収集するビッグデータをAIで分析し、生産ロスやボトルネックに影響している要因の抽出も可能です。作業員のスキルに依存することなく、高度なレベルで分析業務を標準化することが期待できます。
管理業務の高精度化・効率化・標準化を進め、4M管理のSDCAサイクルを継続的に回転させるために、IoTやAIなどの導入を検討すべきでしょう。
まとめ
製造業の発展を支えてきた4M管理は、品質管理の基本として重要視されています。さらに現在では、より一層の効率化・高精度化を目指して、デジタル技術の導入も普及。継続的な改善による自社製品の品質管理水準の向上は、競争優位性や生産性の観点からも軽視できません。
自社の管理手法や技術、体制の見直しを推進するためにも、IoTやAIなどの最新テクノロジーの知見、実績のある専門家に相談することから始めてみてはいかがしょうか。
関連ソリューション・サービス