サイト内の現在位置
コラム
リードタイムとは?
意味や短縮方法をわかりやすく解説
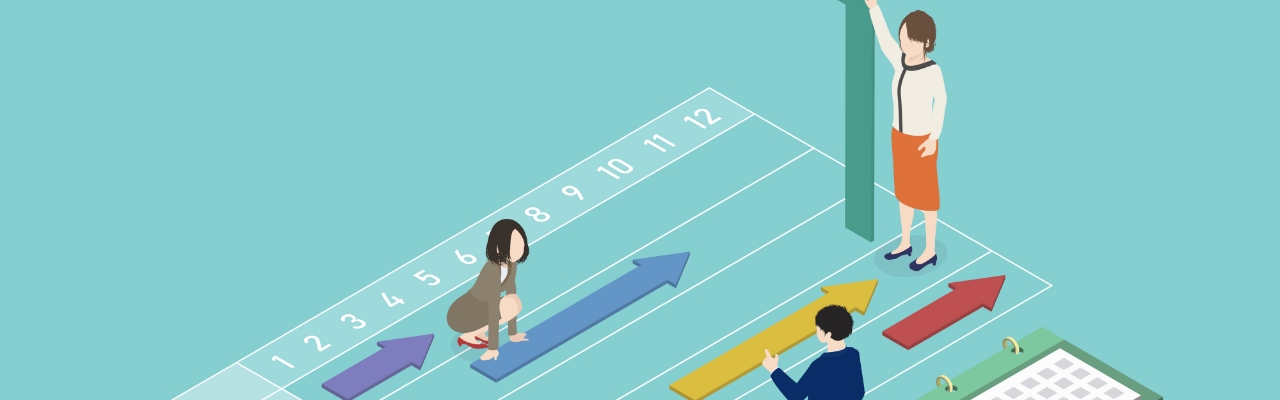
UPDATE : 2022.10.14
リードタイムとは、作業工程の始めから終わりまでにかかる期間を示します。リードタイムの短縮は、キャッシュフロー改善やサービスの差別化につながるため、製造業や物流業などの業種を問わず、ビジネスで重要視されています。
そこで本記事では、企業活動の重要課題であるリードタイムの基礎知識や短縮のメリット、短縮方法、有効策の事例をわかりやすく解説します。
INDEX
- リードタイムとは
- 【開発リードタイム】
- 【調達リードタイム】
- 【生産リードタイム】
- 【物流リードタイム】
- 【トータルリードタイム】
- リードタイム短縮のメリットと重要性
- メリット① コスト削減と適応力の向上
- メリット② キャッシュフローの向上
- メリット③ サービスの差別化を強化
- リードタイムの関連用語
- リードタイムと納期の違いとは
- タクトタイムとサイクルタイム
- 作業の標準時間(スタンダードタイム)とは
- リードタイムの計算と活用
- 生産リードタイムの計算とスケジューリング
- 調達リードタイムと安全在庫
- リードタイムの短縮方法や有効策の事例
- 開発リードタイムの短縮方法
- 調達リードタイムの短縮方法
- 生産リードタイムの短縮方法
- 物流リードタイムの短縮方法
- 生産形態とリードタイムの関係
- リードタイム短縮の注意点
- リードタイム短縮とDX
- まとめ
リードタイムとは
リードタイム(Lead time)とは、工程や作業の始めから終わりまでにかかる所要時間(期間)を表します。製造業における「手番(手配番数)」「先行日数」「基準日程」と同じ意味合いで使われる言葉です。
リードタイムの始点と終点は、業種や場面により異なります。例えば、宿泊業界におけるリードタイムは「予約成立からチェックインするまでの期間」を示す言葉として共通認識されています。そのほか、製造業では下図のようにリードタイムを細分化し、業務改善の指標として活用しています。
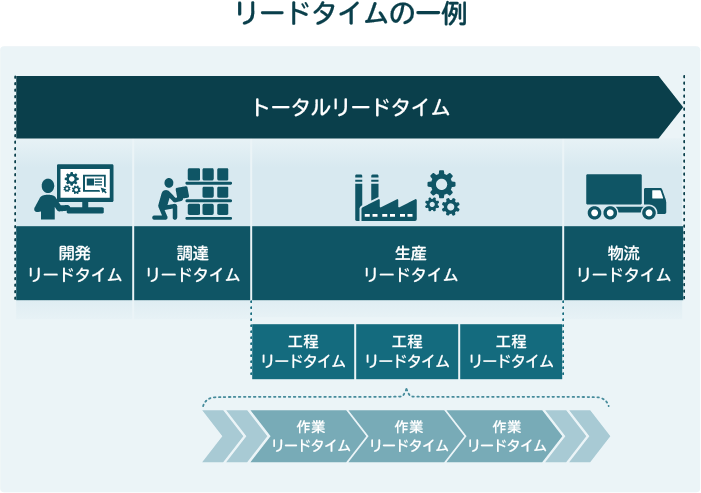
ここでは、ビジネスのプロセスごとに細分化されたリードタイムを、個別に解説します。
【開発リードタイム】
開発リードタイムとは、製品の企画から製品・工程設計までのプロセスに要する期間を示します。製品のコンセプトを実現するために設計・試作・実験を繰り返して細部を詰めていく“詳細設計”と、工場や生産ライン・金型などを作り込んでいく“生産準備”のプロセスが含まれます。
なお、一概に受注生産と分類しても、生産方式によりリードタイムの内訳は異なります。例えば、ゼロからの企画設計を前提とする「個別受注生産(ETO)」では開発リードタイムが発生しますが、既存の製品仕様に基づいて繰り返し製造する「繰り返し受注生産(MTO)」では開発リードタイムが発生しません。
【調達リードタイム】
調達リードタイムとは、発注から納品までに要する期間を指します。顧客目線での“発注から納品までの期間”という意味で、「納品リードタイム」「発注リードタイム」「購買リードタイム」と言われるケースもあります。
製造業における調達リードタイムは、製造用の原材料発注から納品・受入検査を経て、製造現場に納入されるまでの“調達プロセス”全体における期間を示します。そのため調達リードタイムは、原材料の発注から納品までに要する「納品リードタイム」、納品から受入検査までの「受入リードタイム」、検査期間を表す「検査リードタイム」から構成されます。
調達リードタイムは、在庫発注管理における判断材料としての役割もあります。例えば、調達リードタイムが長い状況や安定しない状況からは、「在庫管理コストを肥大化させてしまう恐れがあるが、機会損失を避けるため原材料在庫を多く抱える 」といった判断を下す場合があります。加えて、調達する材料が“製造品”である場合は、調達先における生産リードタイムを考慮した調達計画の立案も必要です。
【生産リードタイム】
生産リードタイム(製造リードタイム)とは、製品製造を開始してから完成に至るまでの期間を示します。生産リードタイムは製造工程ごとの「工程リードタイム」と、各工程を構成する作業ごとの「作業リードタイム」に細分化できます。
生産リードタイムには、加工・組立作業そのものの所要時間のみならず、各工程間の停滞時間(待ち時間・運搬時間・検査時間など)も含まれます。停滞時間は、生産リードタイムの中でも改善の余地がある“ムダな時間”になっている可能性が高い要素です。生産リードタイムの長期化は、仕掛在庫(製造途中の製品在庫)の多量化につながり、在庫管理の負担増や在庫スペース圧迫を引き起こす恐れがあります。
【物流リードタイム】
物流リードタイムとは、製品の出荷指示から納品先へ配達されるまでに要する期間を示します。物流リードタイムは、出荷指示からピッキング・検品・梱包等を経て出荷されるまでの「出荷リードタイム」と、出荷してから配達が完了するまでの「配達リードタイム(輸送リードタイム)」に細分化できます。
物流システムや機械設備による出荷配送作業の効率化や、高頻度の小口配送の実施は、物流リードタイム削減につながります。しかしながら、物流リードタイムと物流コストがトレードオフの関係にある点は留意が必要です。
【トータルリードタイム】
トータルリードタイムとは、ビジネスプロセスにおける始点から終点までの“全期間”を示します。“全期間”の定義により、トータルリードタイムの内訳はケースバイケースです。例えば、製品を受注してから生産・納品するまでの全期間を対象とする場合、トータルリードタイムは「納品リードタイム」「顧客リードタイム(顧客が発注してから製品を受け取るまでの期間)」と同義です。
そのほか、製造業ではトータルリードタイムと誤解しやすい名称のリードタイムがあります。それが、製品オーダーから完成品出荷までの期間を示す「製品リードタイム」「総合リードタイム」「累積リードタイム」です。これらは、完成品出荷後の物流を“対象としない”ため、厳密にはトータルリードタイムと区別できる言葉です。企業でリードタイムを扱う場合は、期間を明確に定義したうえで、組織で共通理解しやすい名称で運用するべきでしょう。
リードタイム短縮のメリットと重要性
リードタイムの短縮には、大別して下記の3つのメリットがあります。
- コスト削減と適応力の向上
- キャッシュフローの向上
- サービスの差別化を強化
メリット① コスト削減と適応力の向上
製造工程間の停滞時間短縮は、製造途中の仕掛在庫を削減します。在庫の減少は、管理工数と人員の適正化につながり、在庫管理費などの人的コスト削減をもたらします。また、余剰在庫に割り当てていた保管用スペースを不要にする点でも、コスト削減に役立ちます。
リードタイム短縮施策として、待ち時間や運搬時間など生産性を高められていない作業工程を削減すると、手が空いた作業員や機械を別の作業に充てられます。柔軟な人員配置や生産計画により、作業効率および工場全体の生産性を高められるほか、増産や生産抑制などの需要変動に対してもスムーズに適応できるようになります。
メリット② キャッシュフローの向上
リードタイムの短縮は、受注から納品、キャッシュの受け取りまでの期間を短くし、キャッシュフローを改善します。さらに、過剰な仕入・在庫の抑制は、ムダな資金流出を防ぎ、資金繰りに貢献するでしょう。キャッシュフロー改善により十分な運転資金が確保できれば、突然の増産依頼にも対応しやすくなります。過剰在庫による資金繰りの悪化が原因で倒産してしまうケースもあるため、「在庫削減×キャッシュフロー改善」は持続的な経営を目指すうえでも重要なポイントです。
また、製品の短納期化は、投入資本の早期回収を促します。リードタイム短縮により捻出されたキャッシュを、機械設備や人材開発への投資に回して生産力を底上げできれば、将来的な売上や利益の増大が図れます。
メリット③ サービスの差別化を強化
昨今は、短納期化がサービス差別化の観点で重要視されています。例えば、Eコマースにおいては“即日発送”や“即日受け取り”を強みにする事業者が増加しています。品質での差別化が困難な場合、長納期による機会損失のリスクは軽視できないでしょう。
納期は、製造業の生産管理で重要視されているQCD(Quality:品質、Cost:コスト、Delivery:納期)の構成要素です。かねてより、納期は「競争優位を獲得するための差別化ポイント」として位置付けられています。特に、部品製造を担う企業は短納期が強みになります。部品製造企業の顧客にとって、部品調達の短期化はトータルリードタイムの短縮につながるからです。
リードタイムの関連用語
ここでは、リードタイムの理解や活用に役立つ関連用語を解説します。
リードタイムと納期の違いとは
納期とは、納入期限の略で、製品を納入すべき期限を示します。リードタイムは開始から完了までの期間を表すため「○日間」などと表記しますが、納期は特定の日付を表すため「□月△日まで」などと表記します。
また、期日と期限の違いも正しく理解すべきでしょう。期日は特定の日時を納入日として“指定”するのに対し、期限は当該日時“まで”の納入を認める言葉です。意味と用途が異なるため、顧客とのコミュニケーションで齟齬が発生しないように使い分ける必要があります。
タクトタイムとサイクルタイム
タクトタイムとサイクルタイムは、リードタイムと同じく製造現場で必須のキーワードです。ここでは、リードタイムと混同されやすいタクトタイムとサイクルタイムの意味や計算・判断方法を解説します。
タクトタイム(TT:Takt Time)とは、1つの製品完成までにかけられる時間のことで、製品の必要数を基に算出する指標です。タクトタイムは、ムダのない作業を実現するために不可欠な要素として知られており、製造業で重視される「標準作業の3要素」※の1つに数えられています。タクトタイムは以下の計算式で算出できます。
タクトタイム = 稼働時間 ÷ 生産“必要”数
※標準作業の3要素:タクトタイム、作業順序、標準手持ち(必要最小限の仕掛品)の3要素のこと。これらが揃ってはじめて、手順にムダのない効率的で安全な“標準作業”が実現するとされている。
サイクルタイム(CT:Cycle Time)とは、1つの製品における製造工程の始まりから完了までの1サイクルで、実際にかかった時間を指します。サイクルタイムは、以下の計算式で算出します。
サイクルタイム = 稼働時間 ÷ “実際”の生産数
タクトタイムは生産計画の指標となる値として、サイクルタイムは現状を表す実測値として、リードタイムは総合的な所要時間として活用され、それぞれが判断基準として機能します。特に、タクトタイムとサイクルタイムの比較は、現状分析の足掛かりになります。例えば、サイクルタイムがタクトタイムを超過している場合は、「ボトルネックとなる工程が発生している状態で、原因追及と問題改善が必要」と判断できます。
タクトタイム = サイクルタイム | 基準となるタクトタイムと実測値であるサイクルタイムが等しい場合は、必要個数を想定通りの時間で効率的に生産できている状態。 |
---|---|
タクトタイム < サイクルタイム | サイクルタイムがタクトタイムより長い場合は、想定よりも時間をかけている状態。生産能力が目標に追いついていないため、製造プロセスで遅延が生じている原因の追及と改善が必要。 |
タクトタイム > サイクルタイム | サイクルタイムがタクトタイムより短い場合は、目標より生産能力が高まっている状態。過剰在庫のリスクもあるため、生産能力が向上した要因を特定して、状況により作業工程や人員配置を見直す必要性がある。 |
作業の標準時間(スタンダードタイム)とは
標準時間(ST:Standard Time)とは、標準的な条件下でかかる作業時間を表します。標準時間は、作業の標準的な所要期間である標準リードタイムおよび生産計画を設定する際にベースとなる指標です。なお、標準的な条件とは「当該業務に適性があり、一定の熟練度を有する作業者が、正常な作業方法・正常な作業スピードで業務遂行する場合」を想定します。
標準時間は、下表のように主体作業時間と準備段取作業時間で構成されます。そして、それぞれに正味時間(主作業・付随作業)と余裕時間(作業・職場・個人・疲労)が存在します。
主体作業時間 | 正味時間 | 主作業 | 機械操作、組立作業など |
---|---|---|---|
付随作業 | 検測作業など | ||
余裕時間 | 作業 | 機械の調整・掃除など | |
職場 | 打合せ、整理整頓など | ||
個人 | 水分補給、トイレなど | ||
疲労 | 休憩など | ||
準備段取作業時間 | 正味時間 | 準備、後始末、段取、運搬など | |
余裕時間 | 休憩など |
標準時間を算出する際は、正味時間に占める余裕時間の割合を意味する“余裕率”を活用します。下記の2つの計算式で、標準時間を算出できます。
【外掛け法】
余裕率 = 余裕時間 ÷ 正味時間
標準時間 = 正味時間 ×(1+余裕率)
【内掛け法】
余裕率 = 余裕時間 ÷(余裕時間+正味時間)
標準時間 = 正味時間 ×{1 ÷(1−余裕率)}
標準時間の測定および設定方法には、実測形式の「ストップウォッチ法・ワークサンプリング法」や、論理的に計算する「PTS法・標準時間資料法・実績資料法」などがあります。実際の作業時間を基にするストップウォッチ法では、熟練度や作業条件などから算出するレイティング係数による補正処理が必須です。一方、PTS法であれば「精度は高いが分析に時間を要する」や「短サイクル作業に向いている」などの特徴があります。
標準時間は、リードタイムや生産計画設定の基礎となるデータです。手法ごとに異なる「実施の容易性・精度・向いている作業」などの特徴を見極めたうえで、作業に合う設定手法を選択しなければなりません。
リードタイムの計算と活用
ここでは、製造業における生産リードタイムと調達リードタイムに焦点を当てて、計算方法と活用場面を解説します。
生産リードタイムの計算とスケジューリング
生産リードタイムを算出するには、製造工程の構成要素を洗い出して合算する必要があります。製造工程の構成要素は、実際に作業を行う加工時間と、作業間の停滞時間に大別されます。そこから細分化すると、加工時間は組立作業や機械操作などの主作業時間と、検測作業などの付随作業時間に分類できます。停滞時間は、待ち時間や後処理時間、運搬時間など、付加価値の無い作業が含まれます。下記は、加工時間と停滞時間で算出するリードタイムの計算式です。
生産リードタイム
=加工時間+停滞時間
=加工主作業時間+加工付随作業時間+待ち時間+後処理時間+運搬時間+…
製造業では、標準時間を基に算出するリードタイム(=基準日程)を、生産計画のスケジューリングに活用しています。
スケジューリングでは、着手した日から順に工程をスケジューリングするフォワード方式と、納期から逆算して作業着手日を算出するバックワード方式があります。フォワード方式は前詰めで工程を進めるので全体の稼働率を高めやすいというメリットがあります。一方、バックワード方式には、仕掛在庫の低減が見込めるというメリットがあります。それぞれ一長一短あるスケジューリング方式であるため、案件ごと複合的に使い分けて“良いとこ取り”する方法も有効です。
現在は、多くの現場で生産スケジューラーというITシステムの導入が進み、機械や人員の稼働にムダの無いスケジューリングが“効率的”に実現しています。作業工程ごとのリードタイムは、生産スケジューラーが役割を果たすための基礎情報として機能しています。
調達リードタイムと安全在庫
調達リードタイム(発注リードタイム)は、在庫管理の最適化に役立てられています。欠品を防ぐために最小限保持すべき在庫である安全在庫は、調達リードタイムを用いて以下のように算出可能です。
安全在庫数
= 安全係数 × 使用量の標準偏差 × √(調達リードタイム+次回発注までの発注間隔)
※安全係数は欠品許容率を係数にした値。例えば、欠品許容率が5%であれば、安全係数は1.65となる
こうして算出された安全在庫数は、企業が持つべき「適正在庫」の算出に利用できます。
適正在庫 = 一定期間の需要数 + 安全在庫数
なお、調達リードタイムに関しては「安全リードタイム」の設定もポイント。安全リードタイムとは、取引先の納期遅れを考慮して付与するリードタイムです。特に、リードタイムが安定しない場合に有効な処置です。
リードタイムの短縮方法や有効策の事例
リードタイムを短縮するためには、以下の3つの方向性に基づく対策が有効です。
- ムダの洗い出し
- 情報共有や連携の強化
- プロセスの最適化
ここでは3つの方向性を踏まえて、各リードタイムの短縮方法と事例を解説します。
開発リードタイムの短縮方法
開発リードタイムの短縮には「材料や製品仕様の共通化」「技術知見やノウハウの共有施策」「フロントローディング」などが効果的です。部品や製品仕様の共通化は、見積や手配などの作業効率を高め、生産段階での在庫管理もスムーズにします。技術知見やノウハウの共有施策は、過去トラブルをデジタルデータベースで共有する施策が有効。過去の解決策から横展開して、開発段階におけるトラブルの早期解決を図れます。
フロントローディングとは、前倒し可能な作業を開発プロセスの初期段階で進め、効率と品質を高めていく手法です。例えば、3D CADによるバーチャルシミュレーションは、試作工数の削減により開発リードタイム短縮に貢献します。そのほか、同時並行的に各プロセスを進めるコンカレントエンジニアリングも、フロントローディング施策の一環です。
調達リードタイムの短縮方法
調達リードタイムの短縮には「調達業務や生産計画の改善」「サプライチェーンや他部門との連携強化」「サプライヤーの見直し・複数化(マルチソース化)」が有効です。
調達業務の改善は、調達リードタイム長期化の原因(発注漏れや連携ミス、共有ミスなど)が自社にある場合に効果的です。具体的には「BOM(Bills of Materials:部品表)のデジタル化」「在庫ロケーション管理のシステム化」「データ再入力などのムダ作業削減」などがあります。また、調達先の生産能力を超えたオーダーが原因で遅延が生じていた場合には、生産・調達計画の根本的な見直しも必要です。
サプライヤーや他部門との連携強化およびサプライヤーの見直し・複数化は、不測の事態に向けたリスクヘッジの強化になります。緊急の発注や設計変更への対応が必要な場合、調達品で不良があった場合、サプライヤーで欠品が発生した場合などに、真価を発揮する取り組みです。
生産リードタイムの短縮方法
生産リードタイムの短縮には「各プロセスにおけるムダの削減」「作業員の多能工化(マルチタスク化)」「最新機器導入による作業工程の最適化・効率化」などがあります。作業プロセスのムダを特定する際は、下記のポイントをチェックすると良いでしょう。
- 小ロット生産で繰り返し発生する付帯業務
- 待ち時間や運搬時間を長期化する工程手順に合わないレイアウト
- 歩留まりを悪化させる高い不良率
- 内段取りの多さ
※内段取り:機械や作業を一度停止させてから、取り掛からねばならない段取り作業のこと
人材面では、多能工化の促進が有効です。1個流し生産の効率化を助けるほか、現場全体でのリソース最適化を促し、ムダの無いスケジューリングに貢献します。そのほか、最新機器の導入は、抜本的に業務プロセスを変革できる可能性があります。すでに「IoTを用いた製造現場の可視化による原因分析と問題解決」「AIの画像認識技術を活用した高度な検査」「RFIDを活用したトレーサビリティの確保とデータ読取りの効率化」などで、業務プロセスの変革が実現しています。
なお、製造現場のムダ削減に有効とされている考え方に「ECRSの4原則」があります。ECRSは、Eliminate(排除)・Combine(統合)・Rearrange(交換)・Simplify(簡素化)の頭文字。業務改善に取り組む際は「排除→統合→交換→簡素化」の順に進めると効果的です。
物流リードタイムの短縮方法
物流リードタイムの短縮には「業務プロセス(倉庫管理・ピッキング・検品・梱包方法など)の見直し」「IT管理システムの連携・導入」などが効果的です。
業務プロセスの見直しでは「入出荷時の導線に合わせたレイアウト構築」「ハンディターミナルの一括読み取りによる出荷検品やピッキング」「作業効率を高める梱包材・梱包方法の採用」などが有効。最新機器を導入すれば、オーダーに合わせて最適な梱包資材を自動選択するシステムの構築も可能です。
IT管理システムは、WMS(倉庫管理システム)やTMS(輸配送管理システム)が物流現場で重宝されています。倉庫管理と配車計画を高度に連携すれば、効率的な車別ピッキングや仕分け作業が実現します。自社で製品製造を担わないEC事業者では、受注管理と在庫管理のシステム連携や一元管理が効果的です。データ連携により受注から出荷までスムーズに移行でき、リードタイム短縮のほか、ヒューマンエラーの防止にもつながります。
生産形態とリードタイムの関係
製品オーダーから納品に至るまでのトータルリードタイムは、受注生産や見込み生産などの生産形態により異なります。生産形態は、デカップリングポイントと呼ばれる「見込み生産と受注生産の分岐点」(=在庫を保有するタイミング)で下図のように分類可能です。
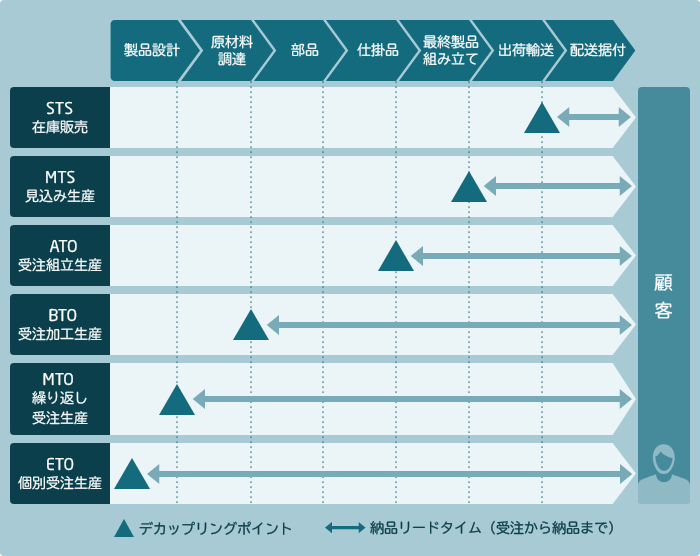
上図で示されているように、顧客との距離が遠くなるほどリードタイムは長くなりますが、在庫量や生産量は減る傾向にあります。生産形態の特徴と顧客需要を考慮したうえで、自社に合う生産形態を選択すると良いでしょう。
STS 在庫販売 |
Sale to Stockの略。小売店の店頭や商品倉庫で在庫し販売するビジネス形態。デカップリングポイントは、最も顧客に近くなる。 |
---|---|
MTS 見込み生産 |
Make to Stockの略。需要予測に基づき相当数を生産・在庫し、小売業者からオーダーが入り次第出荷する形態。リードタイムは短いが、需要予測を誤ると"売れ残り"の在庫を抱えるリスクがある。 |
ATO 受注組立生産 |
Assemble to Orderの略。仕掛品・半製品の状態で在庫し、オーダー後に組み立て作業に移行する。CTO(Configure to Order/ Custom to Order:受注仕様組立生産)とも呼ばれ場合もある。 |
BTO 受注加工生産 |
Build to Orderの略。原材料レベルで在庫し、オーダーに応じて部品製造、組み立て、完成品の仕上げへと移行していく。ATOとBTOは、規格内のカスタマイズやオプション変更に対応するのに向いており、PCや自動車の生産に採用されている。なお、ATO・CTO・BTOが同義として扱われるケースもある |
MTO 繰り返し受注生産 |
Make to Orderの略。オーダーに応じて、原材料の調達から進行する。相応のリードタイムが求められる生産形態。 |
ETO 個別受注生産 |
Engineering to Orderの略。製品の設計から始まる生産形態で、最もリードタイムが長くなる。個別の細かな要求に応えられる生産形態であり、大型建築設備や注文住宅などオーダーメイド対応が必要な商材に採用される。 |
リードタイム短縮の注意点
リードタイム短縮のメリットを最大限享受するためには、下記の注意点を踏まえる必要があります。
- 適正な在庫量のコントロール
- QCDのバランスを崩すリスク
リードタイムを短くできると多量の在庫を抱える必要性がなくなり、キャッシュフローが改善します。しかしながら、環境変化による原材料の調達難や急速な需要拡大などが発生すると、在庫不足で生産が追いつかず顧客の期待に応えられない恐れがあります。そのためリードタイム短縮には、需要予測に基づいた在庫管理が不可欠です。AIを活用した高度な需要予測の導入など、機会損失や失客を防ぐ取り組みにも目を向けるべきでしょう。
リードタイム短縮では「作業員の負荷増大がミスを生み、製品品質を下げてしまう」ケースや「人員投入や機械設備導入の費用対効果が見合わない」ケースも発生しています。いずれも、収益性向上や顧客満足度向上という“目的”ではなく、リードタイム短縮という“手段”にとらわれた結果、QCD(Quality:品質、Cost:コスト、Delivery:納期)のバランスを崩しているケースです。リードタイム短縮に取り組む前提として、設備投資の採算性や短納期化に関する顧客ニーズを把握するための、リサーチや分析・ヒアリングが必要です。
リードタイム短縮とDX
かねてよりビジネスの各現場で “部分最適”なリードタイム短縮が進められていますが、現在注目を集めているのは、組織連携や生産体制を“全体最適”化するDX(デジタルトランスフォーメーション)です。
例えば、IoTやセンサデバイスで工場のデータを可視化するスマートファクトリーは、製造業におけるDXの1つ。機械設備の稼働状況や生産進捗、リードタイムなどのデータ収集により、プロセス全体の業務改善を加速させています。さらに、収集したデータを他部門と連携することで、「物流の最適化」や「顧客データからの販売予測」などに展開可能です。
そのほか、DXによるリアルタイムのデータ共有・連携は、「営業部門による生産能力を超えた受注」や「他部門への伝達漏れ・遅れ」の防止にも役立ちます。組織全体でデータや進捗状況を「見える化」できると、“全体最適”の視点でリードタイム短縮が推進できるでしょう。
まとめ
リードタイム短縮は、コスト削減やキャッシュフロー向上などのメリットをもたらします。多くの企業がリードタイム短縮施策を進めており、中にはIoTやAIなど最先端の技術を活用したDXを実現する企業も現れました。結果として、現在は顧客が求めるリードタイムの水準が高まっています。競合に後れを取らないためにも、専門家の力を借りて、設備投資における採算性の調査から始めてみてはいかがでしょうか。