サイト内の現在位置
コラム
歩留まりとは?
意味や計算方法・改善方法をわかりやすく解説
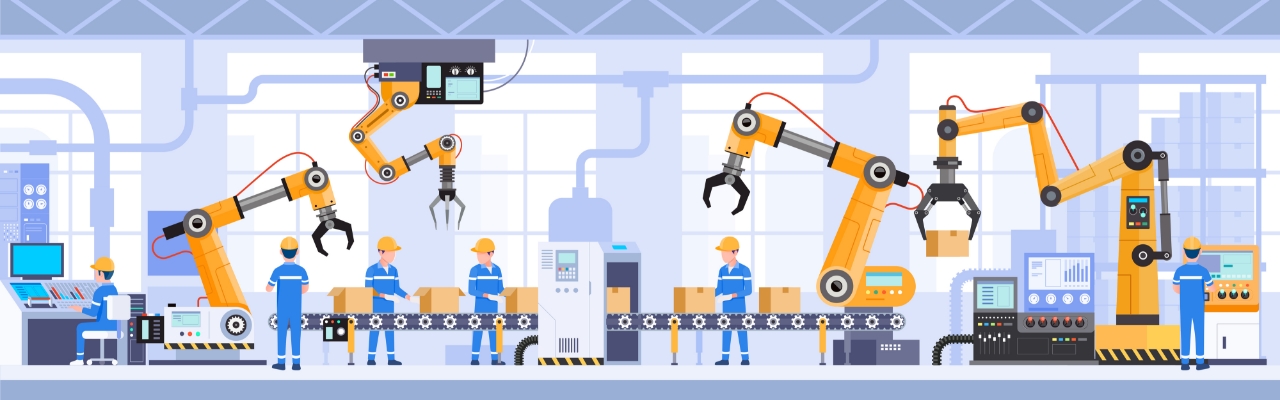
UPDATE : 2022.12.02
歩留まりとは、「全体に対する成果の割合」を表す言葉。製造業では、投入した原料に対する完成品の割合という意味などで活用されています。一方で、採用や営業活動の成果を評価する指標としても普及しています。このように歩留まりは汎用性が高いため、ビジネスで押さえておくべきキーワードと言えるでしょう。
そこで本記事では、歩留まりの基礎知識や計算方法、改善施策の事例についてわかりやすく解説します。
INDEX
- 歩留まりとは
- 歩留まり率の計算方法と活用
- 不良率・手直し率・転用率の計算
- 良品率と直行率の違い
- 歩留まり率から原材料数や原材料費を計算する
- 歩留まりが重要な理由とは
- 歩留まりの改善方法とポイント
- 歩留まりを低下させる原因の特定
- 全員で改善を目指すTPM活動の実施
- 歩留まり向上につながるIT施策事例
- IoTを活用した設備機械の可視化と予知保全
- AIの高度な分析力を活かした不良原因の特定
- ヒューマンエラーを防止するVRとスマートグラス
- 製造場面以外における歩留まり
- 採用活動における歩留まり
- 営業・マーケティング活動における歩留まり
- 水産業界における歩留まり
- その他の業界における歩留まり
- まとめ
歩留まりとは
歩留まり(ぶどまり)とは「投入した原料や素材に対する完成品の割合」や「生産数における良品の割合」などを意味する言葉です。英語では、Yield Rate(イールドレート)と訳されます。言葉の使い方としては、下記の例があります。
- この製品のコストを抑えるためには、歩留まりを向上しなければいけない
- 故障により歩留まりが悪化したので、製造機械を買い換えた
このように歩留まりは、製造業や生産現場を中心に使われてきました。しかし現在では、【歩留まり=全体に対する成果の割合】との解釈により、さまざまなビジネスシーンで応用されています。例えば、採用では「説明会参加から選考に進んだ応募者の割合」を、営業では「見積もりから成約に至った割合」を、歩留まりと表すことがあります。歩留まりは、全体と成果の設定次第で自由に表せるため、同じ会社内でも使われ方が異なる場合があるでしょう。
歩留まり率の計算方法と活用
歩留まりを「全体に対する成果の割合」とする場合、以下の計算式で算出できます。
歩留まり率(%) = 実際の成果数 ÷ 全体の総数 × 100
これを、製造業で使用される「投入原料に対する完成品の割合」や「生産数における良品の割合」に落とし込むと、以下の計算式になります。
【投入原料に対する完成品の割合】
歩留まり率(%) = 完成品数 ÷ 投入原料数 × 100
【生産数における良品の割合】
歩留まり率(%) = 良品数 ÷ 完成品数 × 100 = 良品率(%)
※生産数における良品の割合は、一般的に良品率としても認識されています。
なお、上記の計算式を組み合わせて、投入原料に対する良品の割合を歩留まりと定義することも可能です。例えば投入原料に対する完成品の割合が90%で、生産数における良品の割合が50%の場合とします。この時「100個分の原料からは、90個の完成品」が生産できて「90個の完成品に対して良品は45個」となるため、投入原料に対する良品の割合としての歩留まり率は45%となります。
●不良率・手直し率・転用率の計算
ここでは、歩留まりと併せて把握すべき不良率について解説します。不良率は、「① 生産数(投入数)における不良品の割合」もしくは「② 生産数(投入数)に対して最終的に廃棄になった不良品の割合」を示します。2通りに定義される理由は、一度不良品判定された製品でも手直し作業で良品にできる可能性や、そのほかの製品に転用できる可能性があるためです。つまり、最終的に良品になった数を含む(①)か含まない(②)かで、不良率の定義が異なります。
【① 生産数における不良品の割合】
不良率(%) = 不良品数 ÷ 生産数 × 100
【② 生産数に対して最終的に廃棄になった不良品の割合】
不良率(%) = 廃棄数(不良品数−手直し成功数−転用数)÷ 生産数 × 100
例として、100個生産して10個の不良品が発生し、そのうち5個が手直しで良品となり、2個を別製品に転用できた場合とします。この場合、①の定義では不良率が10%(=10÷100×100)となり、②の定義では不良率が3%(=(10-5-2)÷100×100)となります。
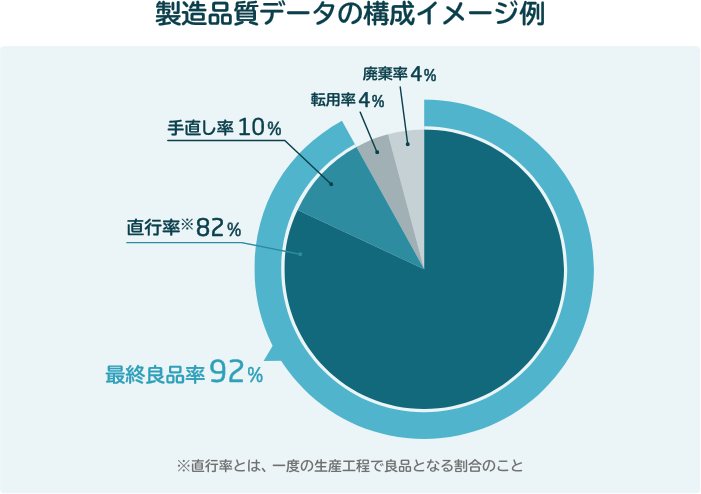
●良品率と直行率の違い
良品率と直行率は、歩留まり率と同じく“生産品質の良さを可視化する”ために役立つ指標です。良品率とは「生産数(投入数)に対する良品の割合」を指します。ポイントは、手直しで良品となった製品を“良品”に含んでいる点です。一方の直行率は「生産数(投入数)に対して、一度の生産工程で良品となった製品の割合」を指します。良品率とは異なり、手直しで良品となった製品が数に含まれません。
【良品率】※良品の定義に、手直しで良品となった製品が含まれる
良品率(%) = 良品数 ÷ 生産数 × 100
= (生産数 – 転用数 − 不良廃棄数) ÷ 生産数 × 100
【直行率】※一度の生産工程で良品と判定された製品を分子とする
直行率(%) = 一度で良品になった製品数 ÷ 生産数 × 100
=(生産数 - 手直し数 – 転用数 - 不良廃棄数) ÷ 生産数 × 100
例えば、100個生産して85個が良品となり、10個を手直しで不良品から良品にできた場合、良品率は95%で直行率は85%となります。生産数における良品の割合を歩留まりと定義した場合、歩留まり率は95%と高い数値になります。しかしながら、手直し作業にもコストが発生するため、製造現場で歩留まりを管理する際には、直行率の改善を意識することも重要です。
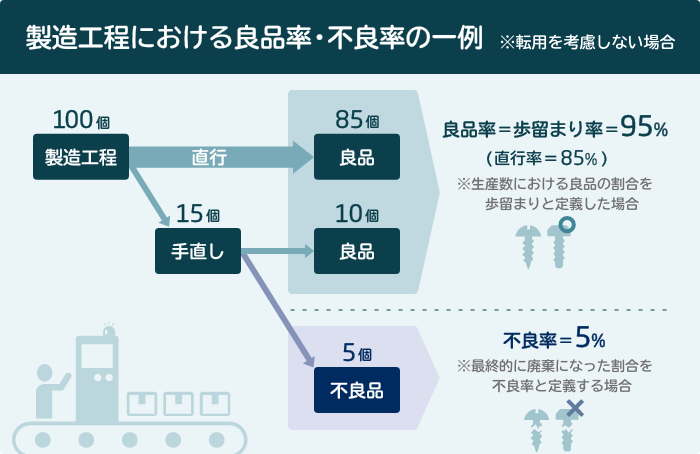
●歩留まり率から原材料数や原材料費を計算する
歩留まり率を活用すると、目標生産数を達成するために必要な原材料数を計算できます。
必要な原材料数 = 目標生産数 ÷ 歩留まり率(%)
例えば、歩留まり率80%の製品を200個作りたい場合、必要となる生産数は250個(=200÷80%)となります。
また、下記の計算式を用いれば、歩留まり率から原材料費を算出することも可能です。
原材料費 = 1㎏当たりの仕入れ価格 ÷ 歩留まり率(%) × 必要kg数
例えば、1kgあたり1,000円の豚肉を加工して歩留まり率80%のソーセージを生産する場合、20kg作るための原材料費は25,000円(=1000÷80%×20)となります。
歩留まりが重要な理由とは
場面によりさまざまに定義される歩留まりですが、全体における成果の割合を示す数値であることには変わりません。歩留まりが低い状態は、目標を達成するために必要な母数が多くなってしまうため、利益率が悪化します。例えば製造業では、不良品の手直しや廃棄にかかるコスト、バッファをもって原材料を調達・保管するコストが発生しています。そのため、歩留まりを管理する取り組みは、利益率の維持・向上を図るうえで欠かせないのです。
歩留まりを継続的にモニタリングできていると、生産段階の異変や問題をいち早く発見できるようになります。不良率や手直し率、直行率などを合わせた分析を深められれば、良品を生産するための条件(仕入れ先や作業担当者、設備など)の特定も容易になるでしょう。特に現在はITの技術革新もあり、製造現場におけるIoTやAIの活用が進んでいます。IoTによるデータ収集とAIによるデータ分析は、歩留まりの管理と分析を高いレベルに押し上げています。
歩留まりの改善方法とポイント
ここでは、歩留まりを改善する際にポイントとなる、下記の取り組みを解説します。
- 歩留まりを低下させる原因の特定
- 全員で改善を目指すTPM活動の実施
●歩留まりを低下させる原因の特定
歩留まりを改善するには、まず歩留まりを下げている原因の特定と改善目標の設定が必要です。製造業における歩留まり低下の原因を把握する時は、4M(Man(人)、Machine(機械)、Material(材料)、Method(方法))の観点から状況整理すると効果的です。
Man(人) | 作業者の知識不足、作業者の加工技術不足、ヒューマンエラー など |
---|---|
Machine(機械) | 機械不良・故障、機械設備の劣化・老朽化、メンテナンス不足 など |
Material(材料) | 仕入れ先の変更、原材料の不良、原材料の大きさのバラつき など |
Method(方法) | 設計ミス、生産プロセス・マニュアルの不備、検査・測定方法の不備 など |
歩留まりが低下する原因は、機械設備の劣化・老朽化からヒューマンエラーまで、幅広く存在します。機械設備の問題は改修や買い替えが必要となる場合もありますが、ヒューマンエラーは教育研修などソフト面の工夫でも改善が見込めるでしょう。解決したい原因と解決策によりコストや負荷が変わるため、「不良やロスに及ぼす影響の度合い・コスト・期間・改善難易度」などから、改善を進める優先順位を決める必要があります。
●全員で改善を目指すTPM活動の実施
TPM活動は、歩留まりの低下を組織全体で改善していく時に役立つマネジメント手法です。TPMとはTotal Productive Maintenanceの略で、「全員参加の生産保全」を意味します。社団法人日本プラントメンテナンス協会は『生産過程で理想とする状態や行動とのギャップをロスと定め、ロスをゼロにすることを目指し、全員が参加して人や設備、企業の体質を改善していく取り組み』とTPMを定義しています。
歩留まり低下の原因となる「不良の発生」や「非効率な原材料消費」などは、TPM活動の改善対象とするロスに該当します。これらのロスの削減と未然防止を組織全員で達成するための指針として位置付けられているのが、下の表でまとめているTPM活動の8本柱です。
TPM活動の8本柱 | |
---|---|
① 個別改善 | 改善対象の設備や生産ライン、生産工程ごとにロスの原因調査と改善を図る取り組み。この個別改善以外の柱は、予防の範疇における取り組み。 |
② 自主保全 | 1人の作業担当者レベルで、製造環境の日常的な保全活動を行えるようにする取り組み。異常事態の迅速な把握と処理、再発を防止して保全環境をより良くするための標準化などの取り組みも求められる。 |
③ 計画保全 | 保全部門が担当して進める保全体制の仕組みづくりを指す。②の自主保全のサポート、設備機械の部品寿命延長、保全費用の最適化、故障発生時のための予備品管理などで、保全活動の効果と効率を向上させていく。 |
④ 製品設備開発管理 | 新規の製品開発時の不良や故障を防ぐために、過去の問題点やロスの原因などの情報を分析して、新しい製品開発システムの構築に活かす取り組み。過去の不良や故障トラブルからの学習不足という組織体質の改善も狙う。 |
⑤ 品質保全 | 製品の不良を発生させないための取り組み。不良が出ない条件の設定と修正、設定条件下での品質管理の徹底、不良につながる要因の分析、原因に向けた事前対策による未然防止などが求められる。 |
⑥ 教育訓練 | 社員個人のスキルを把握し、スキルアップや能力開発、知識習得をサポートする取り組み。教育カリキュラムの用意、OJTやOFF-JT環境の整備、外部セミナーや教材の手配、資格習得支援などで教育体制を整えると同時に、実施効果もモニタリングして継続的に改善していく。 |
⑦ 管理・間接部門活動 | 管理・間接部門活動とは、生産部門のロス削減・低減を支援や、ITシステム導入などの間接部門における管理コスト削減を推進する取り組みのこと。
※管理間接部門とは、営業や企画設計・調達・物流・人事・経理など、生産部門以外の部門を指す。 |
⑧ 安全衛生環境管理 | 災害や健康被害を生まない生産活動を実現するための活動。ヒヤリハットの管理や作業者の健康状態のモニタリング、第三者のアセスメントなどの取り組みで、安全かつ衛生的な環境づくりを目指す。 |
TPM活動は、製造現場における個別の改善活動から始まり、生産システム、コーポレート部門へと組織全体に活動範囲を拡げていきます。なお、TPM活動の個別改善の場面でも、組織全体の場面でも、重要視されているのがIT技術の活用です。次章では、IoT、AI、センシング技術を用いて、高精度かつ効率的に歩留まりを改善した事例を解説します。
歩留まり向上につながるIT施策事例
ここでは、ITソリューションを効果的に活用して歩留まりを向上させている施策事例を、3つピックアップして解説します。
●IoTを活用した設備機械の可視化と予知保全
IoTセンサーを活用すると、機械設備の温度・湿度・振動・圧力などのデータ収集が可能となり、リアルタイムで稼働状況をモニタリングできるようになります。さらに、設備機械から収集するビッグデータの分析により、不具合の兆候が現れた設備を故障する前に補修することも可能です。
これは「予知保全」と言われる取り組みで、現在、製造業で注目を集めているITの活用方法です。データから予兆を検知したタイミングで、ピンポイントに補修できるため、設備機器が機能停止してしまう時間やコストを抑制できます。また、故障に伴う不良品発生(=歩留まりの低下)も抑えられます。加えて、予知保全はITによる管理となるため、保全担当者の能力に依存する属人的な保全作業から脱却できる点もメリットです。
●AIの高度な分析力を活かした不良原因の特定
AIを用いた高度な分析技術は、画像解析による不良品判定の自動化や、不良発生の要因分析を可能にしました。AIの画像解析では、熟練作業者の検査スキルを分析し、製品画像による高度な外観検査を可能に。作業者の違いによる判定のバラつきをなくし、検査の効率化と高精度化をもたらしています。
不良発生の要因分析は、画像解析した不良情報と、生産時の各工程データと組み合わせて分析することで実現しています。AIの高度な分析により、良品率を高められる製造条件を明らかにし、新たな管理基準を設けられます。さらに、IoTと組み合わせれば、不良率などの指標が基準値から外れたタイミングで設備機械の稼働を止めるという自動制御も可能です。
●ヒューマンエラーを防止するVRとスマートグラス
機械による自動化が困難な業務に関しては、VRトレーニングがヒューマンエラー防止に役立っています。VRを活用すれば、現場でなくてもトレーニング可能であるため、実施頻度が少ない業務の習得を助けます。VR空間に熟練作業者のモデルを見本として表示しながら、言語化しにくい技能をトレーニングすることも可能です。また、トレーニングデータを解析すれば、危険な行動パターンを特定できます。
なお、VRは生産ラインの改良や見直しにも活用されています。生産ラインを設計する際にVRを用いれば、準備段階で効果検証ができるため、事前にボトルネック作業を割り出せるようになります。
そのほか、スマートグラスを通して遠隔で未熟練作業者の業務をサポートする技術もヒューマンエラー防止に重宝されています。例えば、現場作業員のスマートグラスに搭載されたカメラを通じて、熟練作業者が現場の状況を確認しながら指導することも可能です。さらに、スマートグラスの録画データは、新人教育や業務の振り返りを行う際にも役立ちます。スマートグラスやVRによるトレーニングは、ヒューマンエラーを原因とする不良品発生の低減につながっています。
製造場面以外における歩留まり
全体に対する成果の割合という歩留まりの概念は、製造現場以外のビジネスシーンでも活用されています。ここでは、「採用」や「営業・マーケティング」など企業活動別の活用例と、「水産業界」など業種別の活用例を解説します。
●採用活動における歩留まり
採用活動における歩留まりは、次の選考フェーズに進んだ人数を成果として定義し活用されています。具体的には「説明会参加人数に対する応募者数」、「書類選考者数に対する一次面接者数」、「最終面接者に対する内定者数」などです。設定項目は連続している必要はないため「応募者数に対する内定者数」という形で採用活動全体の評価も可能です。
【採用活動における歩留まりの計算式】
例① 面接参加者の歩留まり率(%) = 面接選考参加者数 ÷ 書類選考通過者数 × 100
例② 内定者の歩留まり率(%) = 内定者数 ÷ 求人応募者数 × 100
採用活動における歩留まり低下の要因には「選考フェーズが多く、選考期間中に他社で内定が出てしまった」「募集要項との情報不一致」「面接担当者の対応」など、さまざまなパターンが考えられます。どの選考フェーズに問題が生じていて、どのような解決手段があるかを検討するためにも、歩留まりを用いて細分化しながら客観的に分析する取り組みが重要です。
●営業・マーケティング活動における歩留まり
採用活動と同じく、営業・マーケティング活動においても、各取り組みの成果を評価する際に歩留まりが活用されています。具体的には「問合せ数に対するアポイント獲得数」「商談数に対する見積獲得数」などで、営業活動を客観的に評価できます。
【営業・マーケティング活動における歩留まりの計算式】
(資料請求からアポイント獲得に至った割合を歩留まり率とする場合)
歩留まり率(%) = アポイント獲得数 ÷ 資料請求数 × 100
必要な資料請求数 = 目標アポイント獲得数 ÷ 歩留まり率(%)
例えば、アポイントの獲得目標が100件で、資料請求からの歩留まり率が50%だった場合、200件(=100÷50%)の資料請求獲得が必要となります。このように歩留まり率から逆算を繰り返すことで、目標達成に必要なアクションのKPIを算出できます。
なお、実際にマーケティングの成果を管理する際には、ウェビナーやSNS、Web広告やWebメディアなど多様化する動線への対応が必要です。現在では、複雑化する動線を管理するために、SFAやCRM、MAなどのツールが重宝されています。そして、歩留まり率はこれらのツールで管理するKPIの設定に欠かせない指標として機能しています。
●水産業界における歩留まり
水産業界では一般的に、「原材料(魚全体)」に対する「成果物(可食部)」という定義で歩留まりが使われています。魚の種類や状態、用途により、歩留まり率の目安が変わります。例えば、同じ魚でも用途を増やせば可食部が増えるため、アラやカマなどを廃棄せずに加工すると、目安とする歩留まりが変化します。
水産業界では、歩留まりを用いて重量あたりの可食部量を算出し、仕入れや値付けに活用しています。
【水産業界における歩留まりの活用例】
kg当たりの歩留まり原価 = kg当たりの原価 ÷ 歩留まり率(%)
売価 = 歩留まり原価 ÷ 原価率
例えば、1kg当たり1,000円のブリが歩留まり率40%の場合、2,500円(=1,000÷40%)がkg当たりの歩留まり原価となります。そして、この歩留まりのブリを販売する際に、5割の利益率を確保したい場合(=原価率50%)、kg当たりの売価は5,000円(=2,500÷50%)で100gに換算すると500円と計算できます。
●その他の業界における歩留まり
不動産・住宅業界において歩留まりは、不動産販売のプロセスを評価する際の指標として使われています。モデルルームの来場者数や物件案内数と、販売・契約戸数から歩留まり率を算出し、集客や営業活動の改善につなげています。
林業や木材産業では、原材料としての原木から、どれだけの製材を加工できたかを測る指標として歩留まりを活用しています。現在は、環境への関心の高まりやウッドショックの影響もあり、資源のムダが少ない(=歩留まりの高い)状況を追求する動きが重要視されています。
まとめ
全体に対する成果の割合を表す歩留まりは、ビジネスシーンで応用が進んでいる重要キーワードです。特に製造業では、利益率を評価する指標として重宝されています。現在は、IoTやAI、VRなど最新ITソリューションで歩留まりを改善する事例も増加。競合に後れを取らないためにも、抜本的な歩留まり改善を図るITの導入を検討すべき状況でしょう。歩留まりを計測する環境整備も含めて、専門知識のあるITベンダー企業に相談してみてはいかがでしょうか。