サイト内の現在位置
イノベータ’s VOICE
次世代型メンテナンスとして注目される「予知保全」とは
~IoT活用で故障を未然に防ぐ~
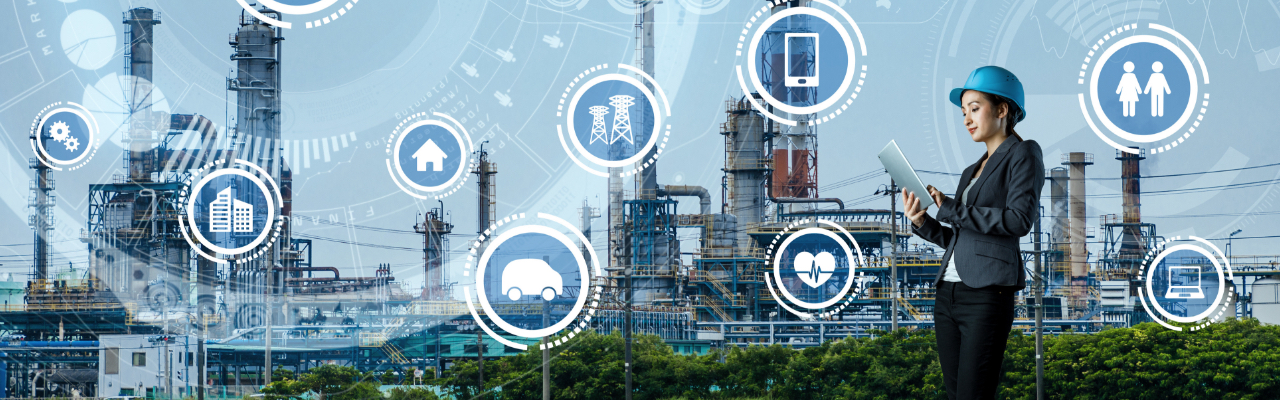
UPDATE : 2021.09.10
生産ラインにおける機械や設備の故障を防ぐために、製造の現場では今「予知保全」が注目を集めています。故障しそうな箇所を先進技術で“予知”し、故障前にメンテナンスする方式です。これまでの保全方式のメリット・デメリットと併せ、次世代メンテナンス「予知保全」の利点を解説します。
INDEX
- 故障前に異常をIoTでキャッチする「予知保全」とは
- おもな保全方式の特徴
- これまでの保全方式におけるおもな課題
- 次世代の保全方式として期待が高まる予知保全のメリット
- 設備の停止時間を最低限に抑えられるため生産性が向上する
- 必要な補修のみ行うためコストを圧縮できる
- 保全技術者の負担を圧倒的に少なくできる
- 保全技術者の技能差による見落としなどが防げる
- まとめ
故障前に異常をIoTでキャッチする「予知保全」とは
今、製造の現場などで「予知保全」が注目を集めています。これは工場設備を安定稼働させるために欠かせない保全活動の最先端スタイル。その名称から分かるように、異常を事前に予知することで、故障を未然に防ぐことが可能です。
機械や設備が故障しそうな部分を予め修理・交換してしまうという方法は、実は以前から存在します(CBM/状態基準保全)。しかし、このやり方は従来のやり方と比べて点検の手間が大きく、「故障しそう」という判断が熟練保全技術者の属人的な勘頼りだったりするなど多くの課題を抱えていました。
結果、これまでは限定的な状況でのみ行われていましたが、昨今の技術の発展により、こうした問題を一挙にクリアできる見通しが立ち、次世代のメンテナンス方式として期待されるようになったのです。
おもな保全方式の特徴
これまで製造現場で行われてきた保全活動の方式について、振り返ってみます。まず、保全活動は故障してから行う「事後保全」と、故障する前に行う「予防保全」の2つに分けることができます。
「事後保全」は、壊れたら直すという極めて原始的な考え方で、修理が終わるまで何もできなくなるという弱点があります。また、故障のタイミングで作っていた製品や部品が無駄になったり、大きな事故を引き起こしたりするリスクもあります。そのため、工場の生産設備など、設備を止めないことを優先する設備では「予防保全」を行うことが一般的です。
「予防保全」は、「時間基準保全(TBM=Time Based Maintenance)」と「状態基準保全(CBM=Condition Based Maintenance)」の2つに分類されます。前者は使用状況、稼働状況を問わず一定期間が過ぎたらメンテナンスするという方法で、後者は部品の状態や稼働状況などを把握し、劣化状況に応じてメンテナンスする方法です。
「時間基準保全」は適切なメンテナンス周期を設定できれば多くの故障や不具合を防ぐことができるメリットがある反面、部品がまだ充分に使える状態でも、機械的に修理・交換するためコスト負担が大きくなるデメリットがあります。なお、「時間基準保全」におけるメンテナンス周期の計測方法は2種類あり、前回の修理・交換からの時間で周期設定するやり方を「定期保全」、設備・部品の累積稼働時間で周期設定するやり方を「経時保全」と言います。
「状態基準保全」は壊れそうな部分だけを見極めて修理するため、「時間基準保全」と比べてコスト面での負担を抑えることが可能。しかしながら前段で言及したように、部品や稼働状況などの把握や故障箇所の見極めに大きな負担が生じるというデメリットがありました。
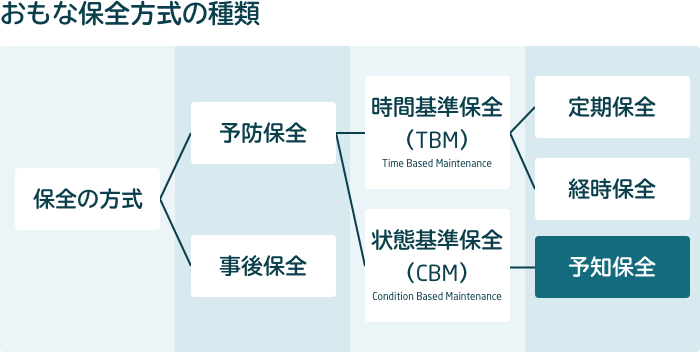
これまでの保全方式におけるおもな課題
前段でも述べたよう、従来の保全方式には次のような課題がありました。
【これまでの保全方式のおもな課題】
- 設備を定期的に一時停止しなければならない(TBM)
- 故障していない設備にも補修をおこなうため、無駄なコストが発生する(TBM)
- 設備のコンディション(状態)把握に手間がかかる(これまでのCBM)
- 設備コンディションの正確な情報が得られない(これまでのCBM)
こうした従来の保全方式の課題をテクノロジーの力で解決し、「状態基準保全」を一歩先に進めたものが「予知保全」です。予知保全では、部品や稼働状況などの把握や故障箇所の見極めにIoT(Internet of Things)やAI(人工知能)技術を活用することで、「状態基準保全」の良いところだけを享受できるようになったのです。
具体的には、IoTは機械や設備の稼働状況やコンディション情報(温度や振動、動作音など)を機材ごとあるいは部位ごとに記録しリモートで集約する仕組み作りに、AIはそうして収集した情報から故障の発生を正確に予知する仕組み作りに活用されています。
次世代の保全方式として期待が高まる
予知保全のメリット
予知保全には次のようなメリットがあります。
【予知保全のおもなメリット】
- ◎設備の停止時間を最低限に抑えられるため生産性が向上する
- ◎必要な補修のみ行うためコストを圧縮できる
- ◎保全技術者の負担を圧倒的に少なくできる
- ◎保全技術者の技能差による見落としなどが防げる
設備の停止時間を最低限に抑えられるため生産性が向上する
「予知保全」では、機械や設備の異常を把握した時だけメンテナンスを行います。そのため、設備の停止時間を最低限に抑えることが可能です。工場設備の稼働率を上げるということはそのまま生産性の向上に繫がります。
必要な補修のみ行うためコストを圧縮できる
「時間基準保全」では、工場設備のコンディションを問わず修理・交換を行うため、メンテナンスコストが高くなりますが、効率的なメンテナンスを行える「予知保全」ならそうしたコストを圧縮することができます。
保全技術者の負担を圧倒的に少なくできる
「状態基準保全」は、定期的な工場設備点検が必要になるため、保全技術者の手間が非常に大きくなります。最新の「予知保全」ではこうした点検作業をIoTを駆使して行うため、保全技術者が工場設備を見て回る必要がありません。人件費の圧縮にも繫がります。
保全技術者の技能差による見落としなどが防げる
最新の「予知保全」では、機械や設備のコンディションをIoTから取得したデータをもとにAIが判断します。保全技術者の熟練度によって差が出てしまいがちだった従来方式と比べて、安定して精度の高い点検が可能です。また、人から人への技術伝承では退職などにより、必ずしもうまく継承されるとは限りません。人からAIへの継承であれば一度で済むため、業務継続という点でも効果があります。
これらの理由によって今、「予知保全」を導入する、あるいは導入を検討している企業が急増しています。
まとめ
これまで熟練保全技術者の存在が不可欠など、極めてハードルの高かった「状態基準保全」が、IoTやAI技術を利用した「予知保全」の登場によって一気に現実的なものになりました。既存の機械や設備に追加するような形で低コストに導入できる敷居の低いソリューションも多数登場しているので、まずはできるところから始めてみましょう。
関連ソリューション・サービス