サイト内の現在位置
目次
品質管理で主に求められることは、工程を正常な形で管理することと不適合品の発生を抑えることです。製品の品質を顧客が求める基準に保つためには、データの収集と分析を行い、問題があれば改善する必要があります。本記事ではその品質管理の基本知識や品質改善において欠かせない分析手法などを紹介します。ぜひ参考にしてください。
品質管理(QC)とは
品質管理とは、一定の品質を保てるように生産工程を検査・検証・保証することです。英語のQuality Controlを略してQCとも呼びます。
生産する際は、納品先・購入先である顧客が求める基準を満たすこと、製造時に不適合品を出さないようにすることが求められます。その要求を満たす取り組みとして、仕入れた原材料などの検査、生産工程の管理・改善・コスト減、完成品に不適合品が混ざってないかの確認を行います。不適合品がある場合は再発防止対策も行う必要があります。もし不適合品の出荷をしてしまうと、事故や健康被害などの大きな問題が発生する恐れがあります。社会的な信用を守り、顧客に安心して製品を利用してもらうためにも、品質管理の徹底は重要です。
品質管理(QC)と品質保証(QA)の違い
品質保証(Quality Assurance)とは、完成した製品が規定の品質を満たしているかを確認することです。納品後のアフターフォローも含みます。企業内で品質管理をしているだけでは顧客側に伝わらない部分が多いため、適切な品質管理をしている証明としてISO9001という国際規格を取得する企業もあります。品質保証と品質管理の違いを挙げると、品質保証の場合は生産~販売後まで活動範囲が及びます。規定の品質で生産する以外に、顧客サービスで安心・満足を提供することも品質保証のうちです。買い手である顧客視点の取り組みという捉え方もできます。一方、品質管理は生産~販売・出荷までを管理する活動のため、業務範囲は生産工程に限られる点に違いがあります。
品質管理(QC)の内容
品質管理を構成する基本的な内容についてわかりやすく解説します。簡単にまとめると品質管理は、主に工程管理、検査・検証、分析・改善の要素で成り立っています。それらはすべて製造の品質を安定化させて、基準に適合するものだけを出荷するための取り組みです。
工程管理
工程管理とは、製造が完了するまでの工程と原料、作業員、設備などを管理することです。一定の品質を保ち、常に効率よく生産することを目的に管理を行います。管理以外では作業者の教育や労働災害を防止する目的もあります。工程管理の主な業務内容は、作業手順の標準化、品質管理・教育、設備の維持と管理、正常な製造工程を維持する管理(見える化)で構成されています。
作業手順の標準化では、品質水準を維持に繋がる最適な作業手順を定めたり、作業手順書にまとめたりします。作業者全員が手順に沿った作業を行うと、品質をより保つことができます。作業手順書に最適なやり方をまとめておけば、全員に同じノウハウを共有できるのもポイントです。品質教育の業務では、作業者に研修やOJTを行います。顧客が満足する品質で生産し続けるためには、現場の作業者に相応の知識と技能を習得させる必要があります。設備の維持と管理で主にするのは、日常点検、修繕・修理、部品交換などです。設備にある異常を早期発見し、故障や労働災害を未然に防止したり、設備のコンディションを整えたりする目的があります。設備が故障してから対応すると、復旧対応に追われて、経済的・時間的な損失に繋がります。設備劣化の放置も労働災害に繋がるリスクがあるため、あらゆるトラブルを未然に防ぐためにも日頃の点検は欠かせません。正常な製造工程を維持する管理は「見える化」「目で見る管理」とも呼ばれます。アンドン、ポカヨケ、インターロックなどの装置を活用して生産現場の異常を可視化し、工程の飛ばしやミス、不適合品の発生を防ぎます。置き場所の間違いがないように定位置を管理する、区分線や色分け区分をする場合もあります。異常が発生していることが、誰から見ても分かるように仕組みを作ることが重要です。
品質検証
品質検証では、仕入れた原材料や部品の検査や製造中・完成後の製品検査をします。検査の種類として受け入れ検査、工程内検査、完成品検査があります。受け入れ検査とは、外部から仕入れた原材料や部品の検査をすることです。そのまま製造に使わずに品質を確認し、不備のない品質の原材料・部品だけを生産工程に投入します。不備のある材料で製造すれば、不適合品の生産に繋がる可能性があるからです。工程内検査では、製造工程の途中で検査を行います。製造途中の製品を定期的にチェックすることで、不適合品が次の工程に流れるのを防止します。例えば、傷やへこみ、汚れなどがないかの外観検査、仕様通りに動くかの機能検査、耐久性はどうかなどのテストをします。近年ではAIの画像認識技術を取り入れた検査も行われています。最終検査(出荷検査)では、出荷しても問題ないかどうかの最終チェックをします。全数検査や抜き取り検査を行い、基準を満たす製品だけを出荷します。不適合品が多い場合は生産工程に問題がある可能性が高いです。そのため、製造プロセス自体を監視することもあります。製造工程の品質は工程能力指数を算出して測ります。
品質改善
品質改善ですることは、製造工程にある問題点の発見、不具合・不適合品などが発生したときの原因特定・再発防止策を立てることです。品質改善の対象は生産工程だけでなく、源流である設計や構築段階も含みます。生産した製品の中には、品質基準から外れた不適合品が混ざることがあります。不適合品を間違えて出荷すると、納品先などに迷惑がかかるため、混入しないように努めなければなりません。品質改善では、事実と直結するデータを土台にして改善策を考えます。データを扱うときは、統計的手法を用いて分析と評価をするのが基本です。品質改善で特によく使う統計的手法はQC7つ道具とも呼ばれます(QC7つ道具については後述)。問題解決や課題の達成にはQCストーリーという進め方が用いられることが多いです。
品質管理(QC)の7つ道具
品質管理のデータ分析で利用される7つの分析手法について解説します。「QC7つ道具」とも呼ばれており、品質管理の基本知識でもあります。状況にあった分析をすることで、品質管理における問題解決や原因の特定がしやすくなるため、覚えておきましょう。
グラフ
グラフは、数同士の割合・比較・大小・推移などを視覚的に表す際に使う図です。数値の羅列で見るよりも、データを視覚的な図で表した方が、数値同士の関係や収集したデータの全体像の把握がしやすくなります。グラフにも種類があるため、目的に応じたものを選択することが大事です。例えば、棒グラフは数の大小の違いを比較するのに適しています。時系列で数値がどう推移したのか把握したいなら折れ線グラフ、割合を見るなら円グラフです。ほかにも帯グラフやレーダーチャートなど様々なグラフがあります。
ヒストグラム
ヒストグラムは度数分布図とも呼びます。棒グラフと似たもので表した図のことです。作成するときは、先に一定の区分/区間/階級に分けたデータを集めて度数分布表を作り、それを図に変換してヒストグラムを作成します。横軸は一定の階級や区分、縦軸が数値を表す度数です。棒グラフと似ていて違う点は、横軸の内容に連続性があることです。データを合算した場合は階級幅に反映されます。ヒストグラムはデータの分布状態を見るのによく使われます。グラフの形状から、製品ごとのばらつきやピーク値などを把握可能です。製造工程ごとのデータを見ることで問題点を発見できます。対策を打ったときの効果確認や現状把握にも便利です。工程が適切に管理されている場合は、ヒストグラムが左右対称に近い形状になることが多いです。
管理図
管理図は、各工程を管理するための折れ線グラフ図です。データを時系列で表示することで、稼働状況を把握できます。管理図が製造現場で使われる理由として、毎日同じやり方で生産していても、品質は常に一定にはならないという点があります。品質が偶然バラつくものは仕方ありません。しかし、異常があってバラついている場合は区別し、解決すべき問題として扱う必要があります。その偶然と異常を区別するツールとして管理図は便利です。工程管理が適切な状態かどうかを調べるのにも使えます。
管理図の作成時は、上方管理限界線、下方管理限界線、中心線(平均値)を示す3本の線を引きます。上方・下方の範囲で折れ線が収まっている限りは安定しているとみなします。範囲外に飛び出た場合は異常があるとして何らかの対処が必要です。管理図に使うデータの種類は計量値と計数値があり、調べる目的に応じたデータを選ぶ必要があります。
パレート図
棒グラフと折れ線グラフを組み合わせた図です。データ値を大きい順に棒グラフで並べ、各要素が全体で占めている割合を累積折れ線グラフに表示します。品質管理で活用する場合は、起きた不具合や事故、クレームの内容別件数や個数などをグラフに表すことで、特に影響が大きい問題をひと目で分かる形で可視化できます。問題の原因・現象を項目別に分類できるため、特に優先して解決すべき問題がどれなのかも分かりやすいです。例えば、グラフを見て、発生件数が多い不具合と稀な不具合があった場合、問題が集中している前者を先に解決した方がよいことが分かります。原因別で見た場合は致命的な問題から片付けるという判断も可能です。多くの問題がある場合にパレート図を使うことで、問題ごとの影響度の把握や解決すべき不具合の優先度を決めやすくなります。
散布図
散布図は、2つのデータに関係性があるかどうかを調べる際に使う図です。縦軸と横軸でそれぞれ別のデータを使うことで、関係性を調べて予測に役立てたり、どんな関係があるのか調べたりすることが可能です。製造においては、製造・加工条件と不良率の関係や品質特性と変動要因の関係などを調べるときに活用されます。散布図で分かるのは2つのデータの関係性だけですが、図から仮説を立てたり因果関係を分析したりするのに役立ちます。データを当てはめる際は、横軸に原因、縦軸に結果を当てはめて散布図を出すのが一般的です。分布の形状から2つのデータの相関関係を把握できます。
特性要因図
特性要因図は、事象を構成する要因を階層構造で整理した図です。図にしたとき魚の骨に似ていることから、フィッシュボーンや魚の骨図とも呼ばれます。使用例として、不適合品の発生が多いという問題(事象)の原因と結果の関連を調べたい場合などに活用します。作成する際は、問題の設定と関連がある要因を洗い出し、図で整理していきます。図を書くときは、矢印を使って要素ごとに分類し、体系的に整理するのがコツです。特性要因を図で可視化することで、数値では見えてこない課題が分かることがあります。図に要因を列挙することで、問題に関連する情報がひと目で把握できる点もメリットです。
チェックシート
チェックシートとは、確認したい項目を設定してデータを記録するためのシートです。主には点検やデータの記録、不適合品の発生調査、事故の予防、安全確保などのために使います。使用例として、点検項目をシートにまとめ、確認漏れがないかのチェックに使えます。記録・調査をする場合は、不正やエラーなどの記録をつけてデータを収集します。つけた記録から、どの項目にデータが集まったのかを見て、分析に活かすことが可能です。記録の仕方は「○・×」の場合もあれば、数値を記録する場合もあります。現場で実践しやすく、シートに記入するだけで簡単に集計できる点がメリットです。記入が負担にならないように、記入方法はシンプルにするのがポイントです。
品質管理(QC)に役立つ手法
QC7つ道具以外の役立つ手法を紹介します。ビジネスシーンでよく使われている手法は、品質管理でも役に立ちます。
PDCAサイクル
PDCAサイクルとは、Plan・Do・Check・Action(計画・実行・評価・改善)というプロセスサイクル回して業務に存在する課題の改善を継続的に行う手法のことです。製造に限らず、ビジネスシーンで幅広く活用されています。もちろん品質管理業務においても役に立つ手法です。サイクルを回すときは、実績、現状の課題や予測、目標とのギャップなどをもとに改善計画を立てて実行し、得られた結果を評価してさらなる改善に繋げます。製造業の場合、不適合品の出荷は避けるべきことのため、製造工程以外に設計段階など上流にも問題がないか、細かく分けてチェックした方がよいです。実行の結果を評価するときは、計画通りに生産が進んだか、上手くいかなかった場合はなぜそうなったかを考えます。よかった部分は今後に活かしつつ、悪かった部分は具体的な改善策に落とし込んでから改善のサイクルを回しましょう。
IE(インダストリアルエンジニアリング)
Industrial Engineering(IE)は、経営資源を効率的に使い、現場の生産性を向上させるための技法です。IEは日本語で言うと生産工学、産業工学、管理工学などとも呼ばれます。科学的な手法で現場の作業工程を細かく分析し、ムリ・ムダ・ムラなく生産活動する最適な方法を考案・設計するのに役立ちます。IEの実践手法は様々なものがあり、分類すると方法研究、作業研究の2つに大きく分かれます。方法研究とは、作業方法を分析し、今よりもよりよい方法を発見するための分析手法です。作業測定は、作業のムダをなくすために、実際に行われている作業を測定・数値化して客観的に分析する手法です。そのほかには工程分析、動作分析、時間分析、ラインバランス分析などがあります。
5S
5Sとは、整理、整頓、清掃、清潔、しつけで構成される活動のことです。名前は各作業名の頭文字であるSから取っています。左から順番に実行することで効率よく実践できます。それぞれの作業内容については、「整理」は必要なものと不要なものを仕分けして処分すること。「整頓」は決まった場所に道具やものを配置すること。「清掃」は掃除とメンテナンスで作業場を点検し、使いやすい状態に保つこと。「清潔」は整理・整頓・清掃の活動できれいな状態を維持すること。そして「しつけ」はほかの4Sを習慣化し、従業員のモラルを向上させることです。5Sを徹底することで、作業効率・安全性の向上、品質・コスト・納期(QCD)の改善といった効果が期待できます。作業環境が良好に保たれていることで、従業員が作業に集中しやすくなるなどのメリットもあります。
4M
4Mとは、生産ラインを正常に稼働させて、適切な品質管理を行うために重要とされる考え方のことです。4Mは人・機械・材料・方法という4つの要素で構成されています。4つの視点から捉えることで、適切な品質管理、変更管理の実現と生産ラインにある問題の発見や改善、事故の予防に繋げられます。
要素について掘り下げると、人(Man)は、作業者のことです。作業者のスキルアップ教育による生産効率の向上や適材適所な人員配置を行うことなどが重要です。機械(Machine)は、生産設備を指します。安定した品質で製造するためにも、定期的なメンテナンス・点検は欠かせません。材料(Material)は、製造に使用する原材料や部品の仕入れ先・コスト・納入先を指します。生産数と仕入れ量のバランスが悪くないか、仕入れた材料の品質チェック体制に問題がないかなどを確認します。材料の発注~調達までのリードタイムや運搬・コストなどを見直すことで流通面の最適化が可能です。方法(Method)は、作業の効率化・安全性の向上を指します。作業手順をマニュアル化することで、業務効率化・品質の安定化に繋がります。
TQC(全社的品質管理)
Total Quality Control(TQC)とは、製造部門に限らず、調達・販売・マーケティングなどの他部門を横断し、連携を取りながら品質管理活動をすることです。言葉自体はアメリカで生まれ、日本にも持ち込まれた結果、日本独自のTQCの形が生まれました。アメリカのTQCの意味合いは「品質管理の様々な努力を、効果的な形でまとめる活動」といったところです。一方、日本のTQCは「全社一丸で行う品質活動」として取り組まれました。品質管理の向上・改善を目的とするQCサークル活動も、日本が改良した結果、生まれたものです。主な活動内容は、従業員を小グループに分け、品質改善についての多様な取り組みを自主的に行い、改善に繋げます。
TQM(総合的品質管理)
Total Quality Management(TQM)とは、トップのリーダーシップをもとにして、経営環境の変化に適した品質管理を行うことです。TQMは、TQCの弱点や限界を乗り越えて発展させたやり方でもあります。TQCは従業員が主体的に動く活動ですが、TQMは経営層のトップダウンという形を取る点で異なります。従業員だけでなく、管理層・経営層など組織の全員が力を尽くすという前提がある考え方です。企業内活動だけでなく、顧客志向の考え方も取り入れられています。活動要素として、新製品・新サービス開発管理、プロセス保証、日常管理、方針管理、小集団改善活動、品質管理教育があります。品質向上だけに注目せず、経営の質やサービス業務など、あらゆる企業活動が対象です。組織のシステムやプロセスから改善を行い、顧客や社会が満足する製品提供を目指します。
SQC(統合的品質管理)
Statistical Quality Control(SQC)は、統計的に収集・解析したデータから品質の基準を定め、品質管理の改善をすることです。SQCを実行することで、品質がバラつく原因の特定と偶然発生したバラつきの区別と排除ができます。データの分析手法としてよく使われるのは、多変量解析法、相関分析、回帰分析などです。QC7つ道具でもあるパレート図、ヒストグラム、管理図なども該当します。実践する際は、状況に応じた適切な分析手法の選択と分析に必要なデータの取得が必要です。適切な分析手法と客観的なデータで判断することで、勘頼みではない事実ベースの改善ができます。データから異常を察知し、問題を早期発見するのにも便利です。
品質管理(QC)を改善し、品質を向上するには
品質管理の改善と質の向上を効率よく行いたいなら、業務のIT化や効率化に繋がるシステム、ソリューションの導入を検討しましょう。
例えば、生産管理、品質管理のITシステムを導入すれば、品質改善に必要なデータの一元管理と活用、業務効率化、業務の実態やデータの見える化、適切なワークフロー管理などが可能です。問題解決や原因の特定の迅速化にも繋がります。問題の発見が遅れれば、顧客満足度の低下や不適合品の生産などによるコスト増が懸念されます。しかし、システムの導入によってあらゆる問題対応を迅速化することで、製造に関連するコストを最小限に抑えることが可能です。システム上に品質情報が集約されるため、改善活動や問題把握に必要なデータをすぐに確認しやすくなります。情報を外部に蓄積することで、属人化の防止に繋がるほか、部署を横断した情報共有の円滑化にも繋がります。システムベースの品質改善体制を構築することで、あらゆる品質管理活動を効率化し、精度の高い品質改善の実現に役立ちます。
まとめ
品質管理とは、生産工程を管理して一定の水準を満たす製品を生産できるように管理することです。品質の安定化や不適合品が発生しないように、品質を改善する取り組みも含みます。品質の改善にはQC7つ道具などを活用したデータ分析が欠かせません。それに加え、製造現場のIT化やICTの利活用による価値の創出が今後の製造業には求められます。
「NEC 製造品質問題管理ソリューション」は、ICTを活用した全社一丸の品質改善体制の構築に役立ちます。品質問題の情報共有を支援する仕組みや問題対応を迅速化するワークフローなどで効率的な品質改善と製造業における課題解決をサポートします。ぜひご検討ください。
ITの利活用を通して生産性を向上させるポイントのホワイトペーパーや弊社のソリューションの資料をご用意しております。無料でダウンロードいただけますので是非ご活用ください。
ITの利活用を通して生産性を向上させるポイントのホワイトペーパーや弊社のソリューションの資料をご用意しております。無料でダウンロードいただけますので是非ご活用ください。
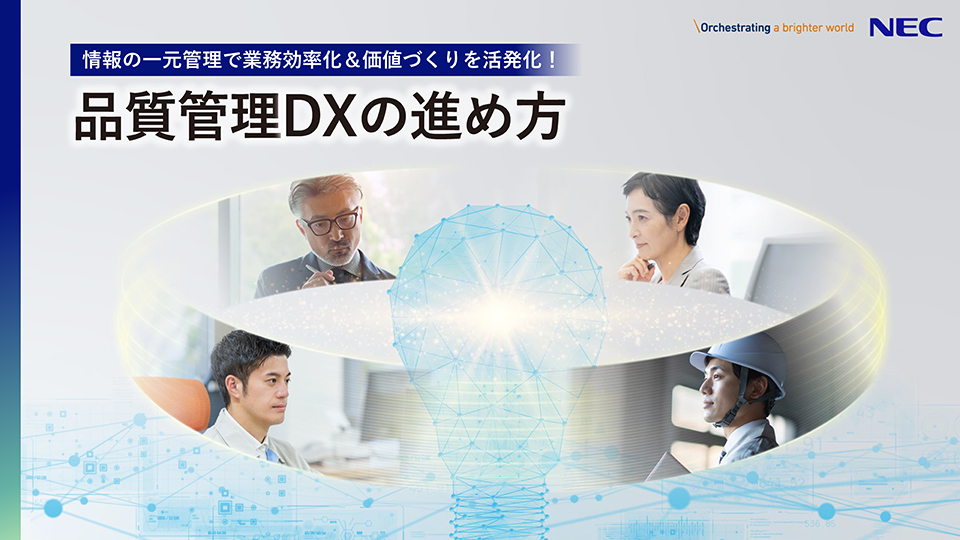
情報の一元管理で業務効率化&価値づくりを活発化!
品質管理DXの進め方
製造業におけるDX(デジタルトランスフォーメーション)は、設計情報のデジタル管理や製造工程のIoTによる可視化など、幅広い領域で取り組みが進んでいます。
市場動向やお客様の状況で変動するニーズを捉え、お客様に満足いただけるよう製品の品質を高めていくために、品質管理のDXで目指すべき姿をご紹介します。
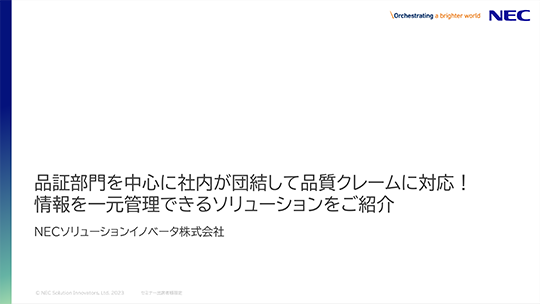
品証部門を中心に社内が団結して品質クレームに対応!
情報を一元管理できるソリューションをご紹介
製造業では、まだまだ、営業・設計・生産・品質部門が縦割り組織の文化が根強く、属人化・情報分散・伝達遅れの問題を抱えているようです。
部門ごとにクローズしている品質情報、アナログデータが混在し評価ができない品質分析の課題を解決するソリューションをご紹介します。