サイト内の現在位置
コラム
原価管理とは?
標準原価と実際原価の違いも解説
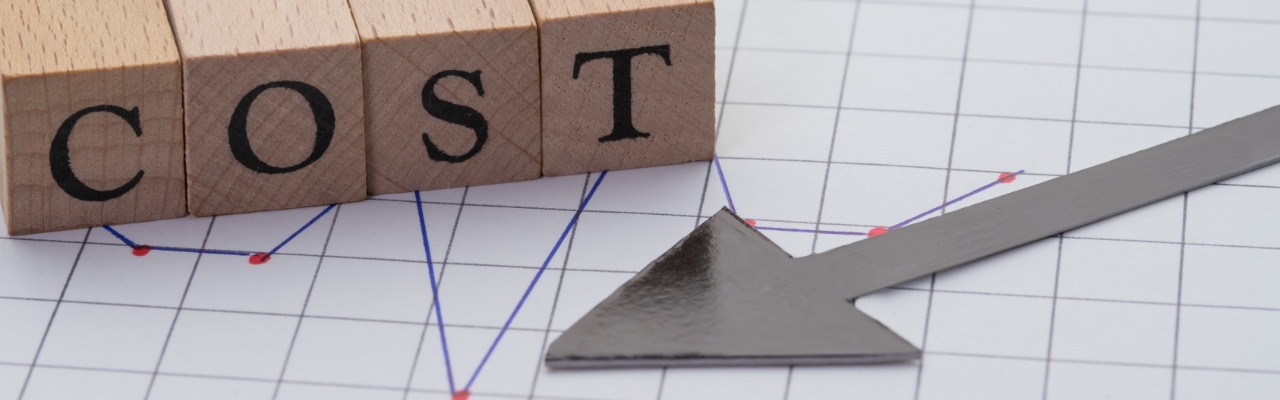
UPDATE : 2025.04.18
原価管理とは、特定の商品の製造やサービスの提供にかかる「原価」の基準を設定し、実際に発生した原価との差異の原因を分析し、改善を進めていく手法です。企業が利益を最大化するためには売上を伸ばすだけではなく、原価管理による原価の最適化が不可欠となっています。そこで今回は原価管理のメリットや進め方、見据えておくべき課題について紹介します。
INDEX
- 原価管理とは
- 原価管理の『原価』とは
- 予算管理との違い
- 原価計算との違い
- 利益管理との違い
- 標準原価と実際原価の違い
- 標準原価の分類
- 標準原価計算とは
- 原価管理を行うメリット5つ
- ①損益分岐点を明確にできる
- ②原価管理で正確な把握と利益率向上を実現
- ③原価変動による迅速な対応とリスク軽減が可能
- ④不要なコストを洗い出し、効率的な運営を推進
- ⑤持続可能な経営計画の策定が可能
- 原価管理の具体的な方法7つを紹介
- ①標準原価を設定する
- ②原価計算の実施を行う
- ③実際原価と標準原価の差異分析の実施を行う
- ④課題改善を実行する
- ⑤差異原因訴求、改善方法を検討する
- ⑥原価改善計画を立案する
- ⑦原価改善計画を実行する
- 原価管理における企業が抱える課題
- 原価を正確に把握するのは容易ではない
- 原価管理の計算には高い専門性が求められる
- 業務の属人化や人的ミスを引き起こしやすい
- システム導入で原価管理をスムーズに効率化
- まとめ
原価管理とは
原価管理とは、特定の製品の製造やサービスの提供にかかるコストを計画的に管理する手法で、コストマネジメントとも呼ばれます。最初に目標となる原価を設定し(標準原価の見積もり)、実際にかかった原価を計算・把握。その後、標準原価と実際原価の差異を分析し、改善活動を行うことが基本的な流れです。原価管理によって適切な原価を把握・管理し、自社の利益向上に結びつけることが最大の目標と言えるでしょう。
原価管理は主に製造業で広く採用されていますが、IT業界、広告業界などさまざまな業界でも活用されている手法です。正確な原価予測は、適切な予算計画や利益目標の設定につながり、経営計画や財務管理においても大きな役割を果たします。
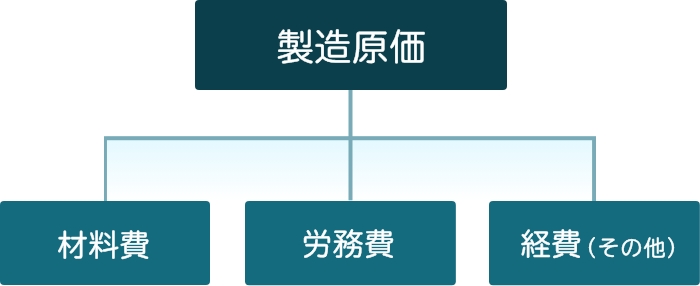
原価管理の『原価』とは
一般的に、原価は「材料費」「労務費」「経費」の3種類に分類できます。
材料費とは、製品の製造に必要な原材料や、部品などにかかる費用のこと。製品一つあたりにかかる費用が明確なものは「直接材料費」、費用が不明確または非常に少額なものは「間接材料費」に分類されます。
労務費とは、製品の生産にかかる人件費のこと。製造部門における従業員の給与が該当します。製品の生産に直接関わる費用は「直接労務費」、間接的に関わる作業や従業員の手当などの費用は「間接労務費」と呼ばれます。
経費とは、その他の費用のこと。外注先へ支払う「外注費」、工場の維持に関わる「減価償却費」、インフラ利用に関わる「光熱費」、現場のネット回線使用料などの「通信費」などが該当します。
予算管理との違い
原価管理と予算管理はどちらも財務健全性を保つ上で重要ですが、焦点が異なります。
原価管理は、製品やサービスの生産過程で発生するコストを詳細に把握し、その削減や効率化に重点を置きます。
予算管理は、企業の総収入・総支出などの実績に基づいて一定期間の予算を策定し、その実行を通じて財務バランスの維持にフォーカスします。企業の予算編成や各事業への予算配分、予算の執行管理などにも活用されるので、原価管理を含めたより広い範囲での管理活動と言えます。
原価計算との違い
原価管理と原価計算は混同されがちですが、目的と範囲において明確な違いがあります。
原価計算は価格設定や財務報告に向けて製品・サービスのコストを正確に算出することに重点を置いています。
原価管理は算出したコストの管理・削減、運用の効率化などを目指すより広範なアプローチを指しています。「コストをどう計算するか」に重点を置く原価計算に対し、原価管理は「計算されたコストをどう管理し、最適化するか」に焦点を当てているのです。
利益管理との違い
企業の利益を最大化することを目的とした利益管理は、売上の最大化とコストの削減を通じて達成されます。これに対して原価管理は、利益管理の一部としてコスト面に注目し、コストの管理と削減を通じて利益の増加を目指す手法です。利益管理は、価格戦略や市場戦略を含んだより幅広い戦略的アプローチを取り、企業全体の財務成績の改善を目指します。原価管理はその中の「1つのカテゴリ」として、製品・サービスに関するコスト削減に特化しているのです。
標準原価と実際原価の違い
原価管理では、標準原価と実際原価の差異の分析が欠かせません。
標準原価とは、製造前にあらかじめ設定した製造原価(予定原価)を指します。製品の製造に伴う材料費、労務費、間接経費について、科学的・統計的に算定。標準原価を実際にかかった費用と比較することで、製造の問題を把握し、解決につなげます。
実際原価とは、文字通り実際に発生した製造原価を指します。まず要素別(費目別)に分類し原価計算を行いますが、このとき、製造に際して実際に発生した金額が実際原価です。これに基づいて原価計算することを実際原価計算と言います。実際原価計算の前に、標準原価としてあらかじめ設定した製造原価(予定原価)を計算する標準原価計算が重要になります。
例えば、月初の製造前にあらかじめ設定した製造原価(予定原価)と、月末に計算した実際原価との間に大きな乖離が発生すること自体は珍しくありません。しかし、この2種類の原価をしっかりと把握できていない企業では適正な原価管理が難しくなります。標準原価と実際原価を比較し、差異を分析しながら定期的に標準原価の見直しと更新を行うことは、企業の利益向上において非常に重要な取り組みになります。
標準原価の分類
標準原価は以下の4つに分けられます。
① 理想標準原価:最も効率良く仕入や製造が行われたときの原価。達成が難しい原価のため、財務関連では用いない。
② 現実的標準原価:現実的な業務から算定した標準原価。達成しやすい原価のため、企業や従業員のモチベーション向上にも繋がる。
③ 正常標準原価:過去の実績と今後の見込みを加味して算定される原価。比較的長期的な目標として利用される。
④ 基準標準原価:経年変化を確認するため、固定的に長期間使用することを前提とした原価。翌年度以降も基準となり、実際に発生した原価との差異分析に用いられる。
標準原価計算とは
標準原価計算とは、標準原価と実際原価の差を分析するために行う計算のことです。標準原価と実際原価の差が発生している場合は、要因を分析してその原因を取り除く必要があります。その際に重要となるのが標準原価計算です。標準原価計算を行えば、請求書の受け取りや棚卸の完了の前に月次決算が可能になります。そこで損益の暫定値をつかめるので、経営判断を迅速に行えるメリットが生まれます。標準原価計算を適切に行い、製造管理を最適化させましょう。
原価管理を行うメリット5つ
正確な原価管理を行うことは企業にさまざまなメリットをもたらします。ここでは「損益分岐点」「利益率の向上」「外部環境の変化によるリスクの軽減」「不要なコストの洗い出し」「持続可能な経営計画」という5つの観点から、正確な原価管理がもたらすメリットを紹介します。
①損益分岐点を明確にできる
損益分岐点を明確にできることは、原価管理の大きなメリットの一つです。損益分岐点とは、利益の黒字と赤字の境目を指します。つまり「これ以上売れれば利益が発生するが、これ未満だと利益が発生せず損失になってしまう」という売上の分岐ポイントです。損益分岐点を明確にすることによって、利益の目標値に対して必要な販売量・製造量も明確になってきます。損益分岐点は、経営方針や、仕入、製造量などの判断を左右する非常に重要な情報なのです。
②原価管理で正確な把握と利益率向上を実現
原価管理によって自社の利益を正しく管理・把握し、収益向上に結び付けることができます。原価を把握することは、適切なサービス価格を設定し、利益を確保する上で不可欠です。逆に原価を適切に把握できていないと、「売上は出ているのに利益が出ていない」といった状況になりかねません。そこで求められるのが原価管理です。自社製品の原価を把握することで、適切な製品価格の設定や無駄なコストの削減を実現し、利益率の向上に向け事業を最適化できるようになります。
③原価変動による迅速な対応とリスク軽減が可能
原価の一つである原材料価格は一定ではありません。世界の経済状況や社会情勢などによって、為替レートや原油価格などは日々変動するためです。原価の変動を考慮しながら経営を行うためには、適切な原価管理が不可欠となります。原材料価格の高騰の可能性など、あらかじめ外部環境の変化を見込んで原価管理を行うことで、原価の変動によって想定される損失や仕入先の変更によるコストなどを算出し、迅速な対応とリスクの軽減が可能になります。
④不要なコストを洗い出し、効率的な運営を推進
原価管理を行うことによって不要なコストが明確になります。その洗い出された不要なコストを削減していくことを、原価低減と呼びます。原価管理の対象となる原価は、先述したように「材料費」「労務費」「経費」で構成されています。それぞれの項目について削減できる部分はないか、一つずつ見直して細かくコスト削減することによって、大きな原価の削減が実現。効率的な事業運営を推進することが可能になります。
⑤持続可能な経営計画の策定が可能
原価管理を徹底すると、原価に関連するさまざまなデータや利益の出し方の目安を知ることができます。材料費、労務費、経費を含めた商品原価や、利益を出すための目安になる損益分岐点をより正確に把握することができるようになるためです。原価や利益に関する解像度を上げることは、長期的かつ現実的な経営計画を立てることにつながります。だからこそ原価管理は経営活動において非常に重要な管理項目の1つなのです。
原価管理の具体的な方法7つを紹介
正確な原価管理がもたらすメリットが明確になりました。では原価管理はどのように進めるべきでしょうか。ここではその具体的な方法について紹介します。
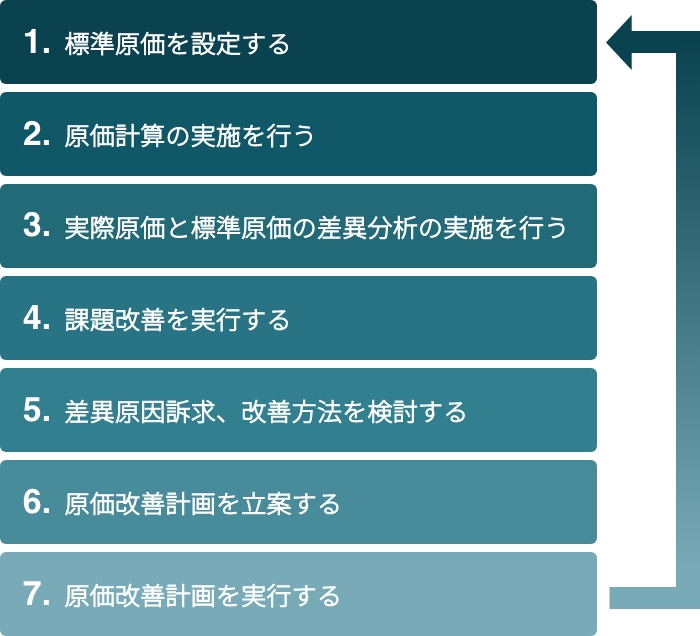
①標準原価を設定する
「材料費」「労務費」「経費」など製造過程で発生する「製造原価」に、製品の販売で発生する「販売費」と、企業組織の維持管理にかかる「一般管理費」を合わせ、原価の総額を計算します。次にその総額から概算で製品1単位あたりの原価を算出。その数値をベースにして、トラブルやアクシデントの発生がなく想定通りに生産された場合の原価を計算し、「標準原価」とします。標準原価は高すぎることも低すぎることもなく、最適な値が水準となるように設定することが重要です。
②原価計算の実施を行う
原価計算は材料費(製品の製造に必要な原材料や部品などにかかる費用)、労務費(製品の生産にかかる人件費)、経費(外注費・減価償却費・光熱費・通信費など、材料費・労務費を除く全ての費用)を合計して割り出すもので、できるだけ正確に行うことが必要になります。いかに小さな金額でも、原価に含まれるものであればすべて計上しましょう。標準原価計算・実際原価計算・直接原価計算という3種類の原価計算を行うことによって、正確な利益が算出されます。
③実際原価と標準原価の差異分析の実施を行う
差異分析のポイントは、直接材料費(製品1つあたりにかかる費用が明確なもの)、直接労務費(製品の生産に直接関わる人件費)、製造間接費(どの製品の製造に消費されたのか明確に区分できないもの)の3項目です。それぞれの標準原価と実際原価との違いを見ることで、事業における課題点が洗い出せます。材料にかかる価格や数量の差異、作業員の作業時間の差異などについて分析するというように、要素ごとに比較していきましょう。
④課題改善を実行する
上記①〜③のフローで分析を行い、課題があれば改善を実行します。例えば差異分析を行った結果、標準原価と実際原価の差異が大きいことがわかった場合、改善できる部分も大きいことが予想されます。実際、差異が大きい部分には課題が潜んでいることは珍しくありません。その課題について「なぜ差が出るのか」を掘り下げることが重要になります。大切なことは、課題が見えてきたら、実際に原価を抑えるための改善活動につなげることです。
⑤差異原因訴求、改善方法を検討する
差異分析によって明確化した課題に対して、まずは改善策を実行するための検討を行います。例えばコスト削減の工夫として、仕入れ先の見直しも含めて「より安価な材質に変更する」、「製品の構造を簡素化して部品の数を減らす」などの改善策が考えられるでしょう。このほかにも、組み立ての工数を減らす、不良品の発生を防いで歩留まり率を上げる、といった改善策も考えられます。
⑥原価改善計画を立案する
原価改善計画は、企業の利益最大化と競争力強化に不可欠です。「購買台帳を作成し、材料費を製品ごとに管理する」「日報をもとに製品ごとに製造工数を精緻化する」「単位時間あたりの人件費を計算して計上する」「データの精緻化とともに見える化を進める」というように、現状のコストを把握し無駄を削減したり、原価改善のための目標を明確にして具体的なアクションを実行したりすることで、財務安定と成長を支えます。
⑦原価改善計画を実行する
原価改善計画を実行するには、案件ごとの利益を見える化し、そこから対策の検討を行うことが必要です。ただし見える化をしただけでは原価低減や利益向上にはつながっていかないため、ITで見える化し、現場の改善活動に繋げていくことが重要になります。
原価管理における企業が抱える課題
上記の流れを踏まえれば必ず原価管理が進められるかと言えば、そう簡単にはいかないことが一般的です。外部環境によって変動する原価を正確に把握することは、たとえ担当者が幅広い知識を持っていたとしても困難を極めます。さらに原価管理が適正に行える担当者がいたとしても、業務の複雑さゆえに属人化する可能性も潜んでいます。
原価を正確に把握するのは容易ではない
原価を正確に把握することは実は非常に難しく、原価管理を行う多くの企業で大きな課題となっています。原価は外部環境のさまざまな要因(社会情勢や為替レートなど)によって価格が大きく変動することは珍しくありません。豊富な経験を積んだベテランの従業員であっても、その変動を把握することは困難を極めます。特に多品種少量生産を行う企業の場合、その難易度は跳ね上がります。また、属人的な原価管理となることでリスクも高まります。
原価管理の計算には高い専門性が求められる
原価管理の計算方法は非常に複雑で、正確な計算には専門知識が必要になります。原材料はもちろんですが、製造に関連する従業員の労務費も含めた計算を行わなければなりません。関連する部門が多くなればなるほど、計算方法の複雑さは増していきます。豊富な経験を持ち専門知識を身につけた従業員であっても、常に原価を正確に把握することには困難が伴います。仮に経験も専門知識も十分ではない従業員が原価管理に携わった場合、後になってから「赤字になることが判明してしまった」というケースも考えられます。
業務の属人化や人的ミスを引き起こしやすい
自社の原価管理を特定の担当者のみが理解している状況の場合、業務の属人化が懸念されます。原価管理はその内容や計算方法が複雑で難しいことから、属人化しやすい傾向にある業務です。担当者自身の業務効率化のためにエクセルに複雑な関数や計算式を組み込むケースがよく見受けられますが、別の担当者に替わった場合にも効率を担保できるとは限りません。このように属人化した状態を放置すると、担当者の異動や転勤、退職によって業務がブラックボックス化し、原価管理が滞るリスクが高まります。
システム導入で原価管理をスムーズに効率化
原価管理の課題を改善する方法として、原価管理システムや生産管理システムの導入が考えられます。
原価管理システムは原価計算から分析、コスト削減までを一貫してサポートするシステムで、現場の実態を的確に反映したデータ活用が可能になります。定型業務を自動化して担当者の負担を軽減し、さらにエクセル管理における属人化リスクも解消できます。
生産管理システムは納期・在庫・工程・原価などの情報を一元管理するシステムです。原価管理システムよりカバー範囲が広く、生産全体の管理機能を備え、より包括的な最適化を実現できます。
現実の原価管理においては完全な実際原価の把握が難しいケースもあります。しかし簡易的に算出した実際原価であっても有効に機能することが多々あります。特に中堅・中小企業では、投資対効果を考慮した柔軟なアプローチが求められるでしょう。このような提案があるかどうかはベンダーの経験や知見に依るところが大きいため、システム導入の検討にあたってはベンダーの選定が重要なポイントになります。
関連情報
まとめ
企業の利益を向上させる上で、原価管理には5つのメリットがあります。実際に原価管理を進めるにあたっては7つのステップを踏まなければなりませんが、業務の属人化など多くの企業が抱える課題があることも事実です。そこで豊富な経験・知見を持ったベンダーとともに原価管理システムや生産管理システムの導入を進め、属人化のリスクを解消し、生産全体も含めた包括的な最適化を目指すことが、これからの企業には求められています。